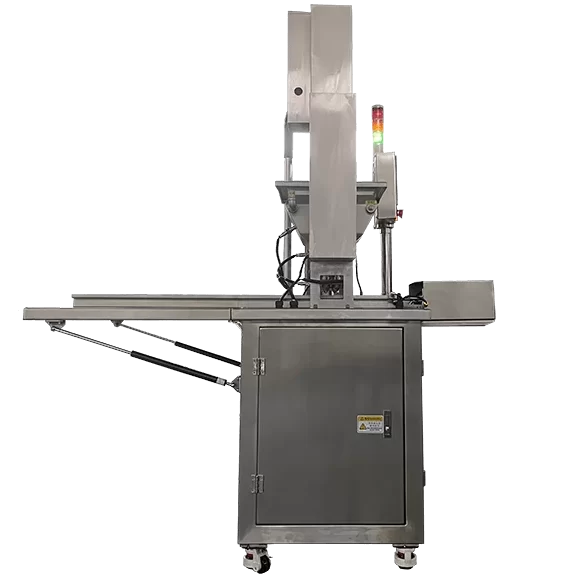
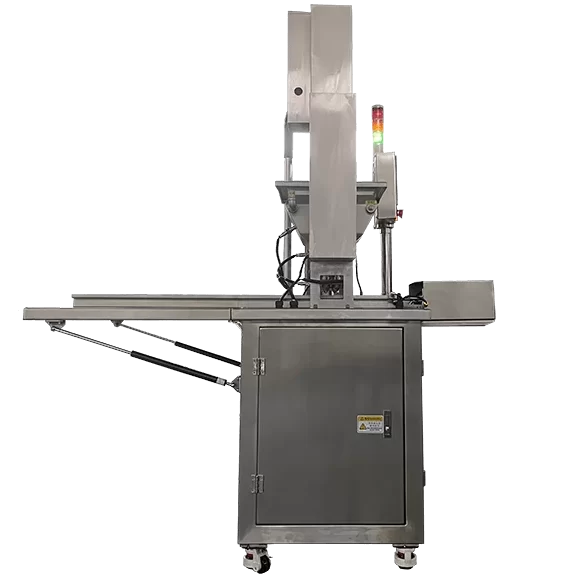
The R&D Gummy Machine is a servo-driven, short-term pouring system
designed for entry-level operation or for experimental and development work in
larger operations. It has a small footprint, low energy costs, and is easy and
practical to move on casters.
As a machine with high temperature, and metal drive, it is important to always prevent personal accidents and protect production and the machine.
1. What is the process flow of R&D gummy machine?
Dissolved sugar is added to the tiltable sandwich pan → manually add the mold into the hopper → PLC control → pouring and forming → cooling →
demoulding.
Note: It should be cleaned in time after not gummy pouring to prevent gummy
from hardening and sticking.
Operation control mode: touch screen.
Human-machine interface language: English or local language is used.
The contents to be displayed on the operation screen (including but not
limited to): hopper temperature, bottom plate temperature, manifold temperature,
pouring volume control, pouring time control, mold pushing time control, can be adjusted on the touch screen.
The control system of the equipment meets the requirements of the electrical
installation code for industrial equipment, and the electrical equipment of the
control system of the equipment meets the requirements of international
certification.
The CIP process is, adding hot water to the tiltable sandwich pot → manually adding funnel into the hopper → PLC control → hot water rinsing, if one cleaning is not enough can be repeated several times, our electrical components are made into separate cabinets to isolate contact with water.
R&D gummy machine can produce one color product with center or two
colors of uniform size.
The indexing conveyor passes the molds through the machine and makes deposits. There is a no mold/no deposition system. The molds are removed from the machine by hand after deposition and set aside to cool. The demolding can be done manually or by a demolding device.
The molds can be either Teflon aluminum molds or flexible food degree silicone . The Teflon aluminum mold is designed with thimble, after the gummy is cooled and formed, press the thimble to push the gummy out of the mold; the elastic silicone mold has a soft bottom that can be pressed directly to push the gummy out of the mold. Mold details
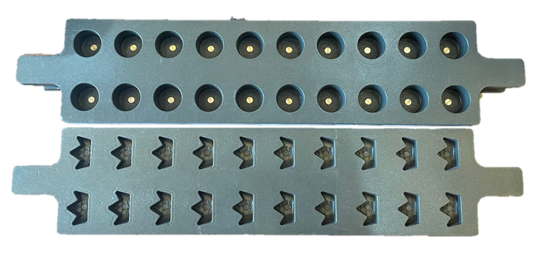
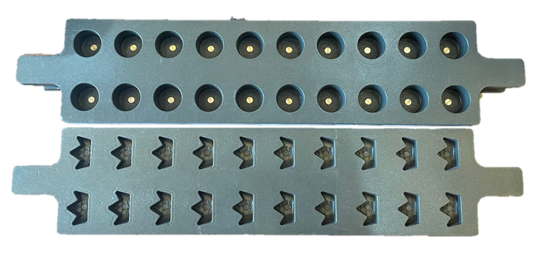
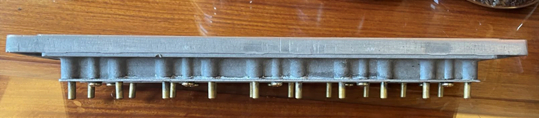
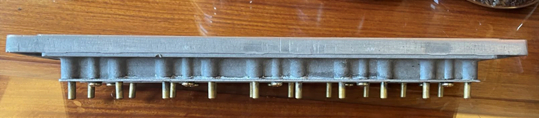
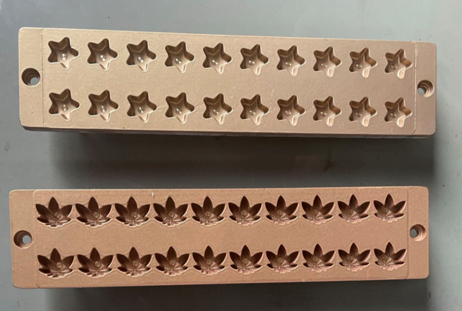
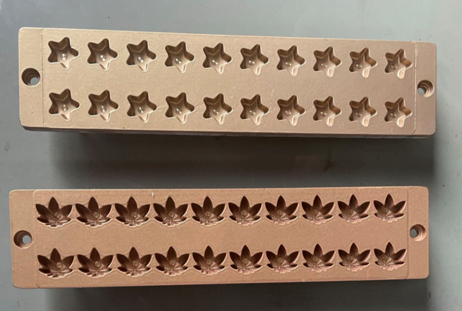
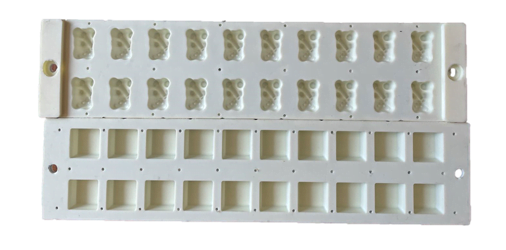
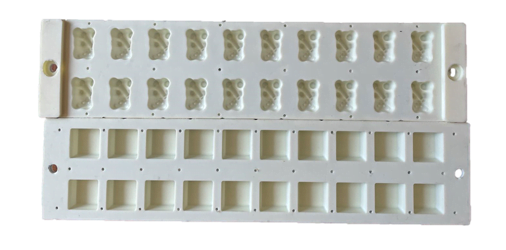
How does the pouring machine carry out the gummy pouring during the
production process?
1、Operator will place the mold on the push mold track and remove the hand
2、Push the foot pedal, push the mold to push the mold to the bottom of the hopper, opposite to the distribution plate
3、When the mold is pushed to the bottom of the hopper, the gummy machine receives the command to drive the servo motor to make the punch rod to move up and down, forming the extrusion, squeezing the syrup from top to bottom into the already placed mold.
(Note: pushing the mold to the designated position first, and then pouring, as a process)
4、Repeat the above steps, push the mold filled with syrup out of the bottom of the hopper to the back section conveying platform.
5、Squeeze the mold with syrup and let it cool.
6、Form the gummy and use the demoulding device for demoulding.
This will give you the molded gummy. Aluminum mold has strong thermal conductivity compared to rubber mold to cool down faster and easier to demold.
2. Name and introduction of each part of R&D gummy machine
Servo motor, punch rod, hopper, distribution board, PLC controller, push mold motor, foot pedal, etc.
Hopper with jacket electric heating and heat preservation, temperature can be adjusted manually in the display. Placing the finished blended syrup.
Servo motor drives the punch up and down. Through the up and down movement of the punch rod, the syrup in the hopper is squeezed and distributed to the mold through the distribution plate.
The pushing mold motor independently controls the pushing mold to push the mold placed by the worker to the bottom of the hopper smoothly.
The foot pedal is used in the order of smoothly placing the mold on the track first, taking care of their own safety to retrieve their hands, and then the foot pedal is stepped on last.
The PLC controller plays an integrated role. When the foot pedal commands, the push mold motor confirms that the mold has been placed and carries out the push mold procedure. While the above conditions are met and there is already a mold under the hopper, the top servo motor starts to drive the punch rod and completes the pouring. When the pouring machine is working, make sure there is material in the hopper to prevent the machine from idling and causing damage to the equipment parts.
There are no sharp edges and sharp corners on any part of the equipment. All parts and welds are chamfered and polished to provide minimum sharp corners, minimum seams and flat and smooth connections, and the overall design fully improves the clean operability of the equipment.
3. Equipment parameters
Food contact parts are stainless steel SUS316L, copper, Teflon material and food-grade PVC material.
The material meets the requirements of health food. Easy to clean, not sticky slats, can be washed. No contact with food is 304 material; no mold no pouring; with recipe management, can store hundreds of parameters, easy to call; bare motor are equipped with protective outer cover, with foldable mold conveying platform at the back, with casters at the bottom.
The operating platform has enough strength to meet enough load of operators and materials to ensure no change of shape, safe and reliable.
When the utility not match the requirement, the equipment will not start or stop automatically. In case of power failure, the machine can be immediately stopped and stabilized to protect the operator, equipment and products. The PLC data can be guaranteed not to be lost after power failure to ensure the program integrity.
When the equipment is abnormal, it can realize the automatic light prompt alarm, the reason prompt on the display, and the gummy machine stops running.
Electrical system configuration international brand.
1、Forming method: pouring and forming
2、Capacity: 20-40kg/h (the speed of placing, affects greatly)
3、Heating method: electric heating
4、Total power: 12-20kw
5、Voltage: 220V/380V
6、Weight: about 350kg
7、the equipment can produce gummy type: Gummy (Monochrome or
Bicolor)
8、Punching rod: 20 Pcs
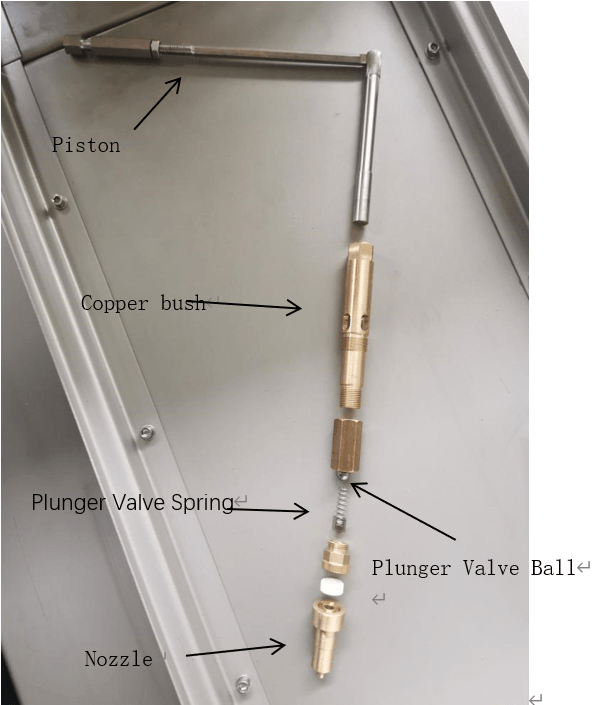
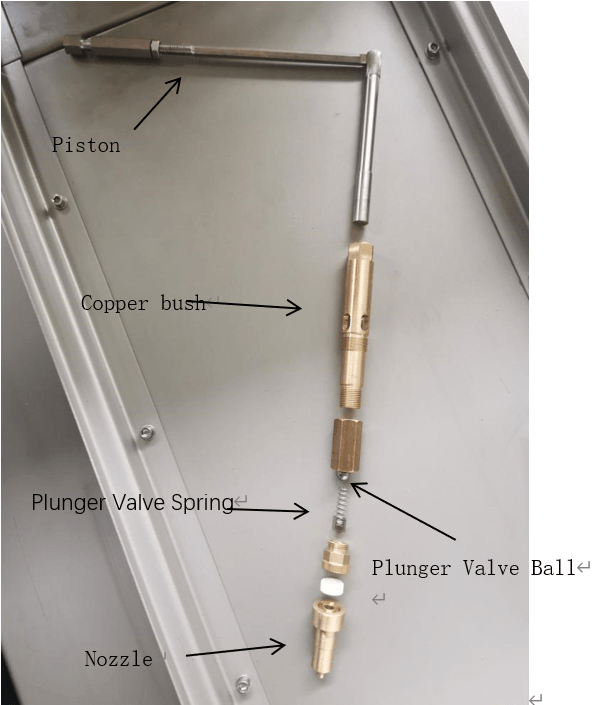
4. What safety issues should be paid attention to during the use of the R&D gummy machine?
As a kind of equipment with high temperature and metal transmission, it is necessary to prevent personal accidents at all times to protect the production and the machine. For the safety of operators and maintenance personnel, turn off all air and power sources during maintenance. Please read this manual carefully and follow the safety standards strictly.
4.1、Safety guidelines
There is a risk of pinching the body and fingers on the drive mechanism of the pouring machine; do not touch the movable part of the machine and the cylinder during operation.
Do not touch the removable part of the machine and the high temperature part during operation.
The power supply and air source must be turned off during inspection and repair, and if the body enters the middle of the moving parts of the machine, the power supply should be cut off immediately.
No matter what the occasion, the operator into the dangerous parts should first cut off the power supply.
4.2、Operator safety
Prevent electric leakage and electric shock
The machine must be well grounded, to ensure that the power grounding wire is correct.
When the machine is connected to the power supply, all operating panels and outer covers should be in the correct position, after the machine is turned on, no contact with electrical appliances is allowed.
Keep the body insulated from the ground: wear protective gloves, safety shoes as well as safety clothing.
Should be equipped with a device that can be quickly disconnected from the power supply
Frequently check whether the housing of the mains is damaged or broken, otherwise it must be replaced immediately
During maintenance, the power switch must be disconnected or the power plug removed first, and wait for 5 minutes (after the capacitor is discharged) before the later work can be carried out to prevent electric shock.
Prevent fire and burn accidents, operators should wear appropriate safety protection.
Keep the machine and its surrounding environment hygienic, safe disposal of waste water.
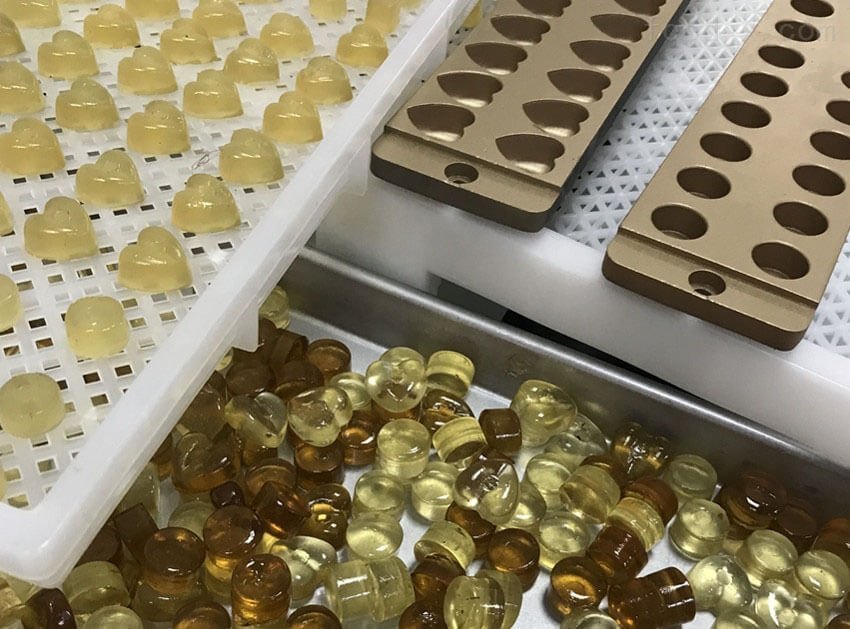
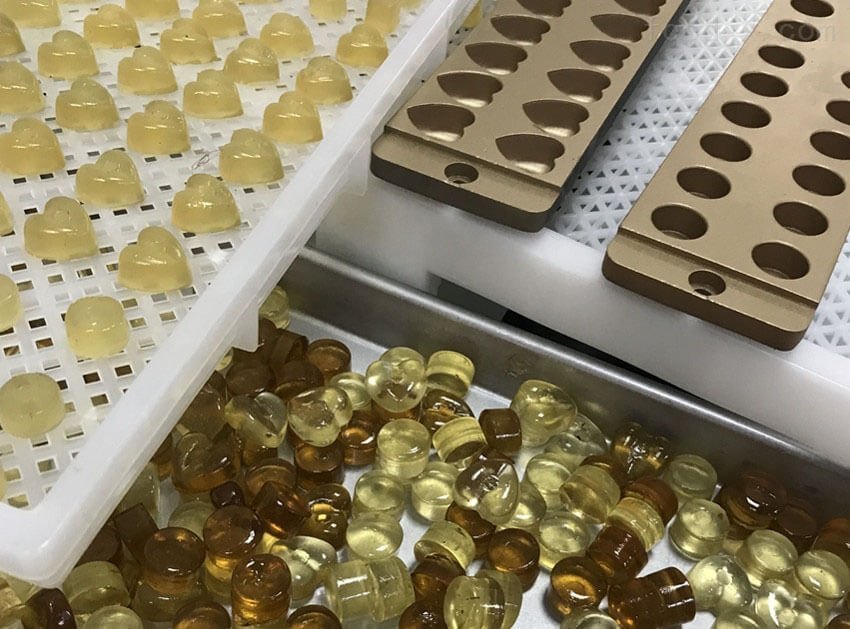
5. Our machines have certain requirements for the use of the environment
1. It is recommended that the workshop be of a fully enclosed structure to prevent dust from the external environment from entering the workshop.
2、The workshop should have ventilation and exhaust fan, and the exhaust fan should be applied with isolation net to isolate the workshop from the outside and prevent the dust in the outside environment from entering the workshop.
3、The board wall should be made of easy-to-clean sanitary materials, and there should be a sanitary ceiling to prevent dust from accumulating and falling onto the machines and products, affecting the hygiene of the products. Can be used in the clean room.
4、It is recommended to install air conditioning in the workshop to ensure the temperature requirement of this equipment to the production workshop (1-40C, 30-55%).
6、Daily maintenance of fudge machine equipment
1.Cleaning
2. The pneumatic part, the two parts need lubricant maintenance, other parts just need to keep neat and tidy
3. use should regularly check the cylinder parts for any abnormalities, find the problem and deal with it in time.
4. check the connection parts for looseness, etc., and the active parts of the cylinder installed by shaft pin should be lubricated regularly.
5. normal working conditions of the cylinder: working pressure should be between 0.4~0.6Mpa, ordinary cylinder movement speed range is 50~500mm/s, ambient temperature control at room temperature. In the case of low temperature, anti-freezing measures are needed to prevent the moisture in the system from being frozen.
7、Summary – Initiate inquiry
Our company has many years of experience in the gummy machine industry, we have a perfect industry chain, quality service, and look forward to your inquiry.