

1. Overview
The falling film evaporator is suitable for the evaporation and
concentration process of liquid materials in pharmaceutical, glucose,
brewing, starch, oral liquid, chemical, food, natural seasoning, food
additive, monosodium glutamate, dairy and other related industries. It is
also suitable for low-temperature vacuum concentration of small batch,
multi-species or heat-sensitive materials and recovery of organic solvents.
This equipment consists of heater, evaporator, condenser, liquid receiver and connecting pipeline valve, etc., which covers an area of small; the
heater adopts heat preservation structure, and the shell is made of stainless steel sheet outside the heat preservation layer, and the surface is made of mirror and matte treatment; (the vacuum system can be used with other
equipment with multi-stage pump and hydraulic ejector or water ring
vacuum pump.)
This equipment is a falling film evaporator. Adopting the combination of
external heating forced circulation and vacuum negative pressure
evaporation, the material is concentrated without foam in a completely
sealed state, with fast evaporation speed and concentration specific gravity
of ~1.3 (solid content of concentrated liquid can reach 78% and pure oil content can reach 98%); the material is heated evenly and the temperature is low to protect the effective ingredients of the material.
This equipment is simple to operate, adjust the feeding valve opening
degree, continuous feeding (can be installed flowmeter), so that the
feeding volume and evaporation volume to maintain a balance. The
material is pumped into the evaporator by vacuum, when the liquid level reaches the visible position of the lower sight glass, close the feed valve, turn on the steam of the heater to make the liquid boil moderately and evaporate, turn on the cooling water (or industrial cooler) and vacuum valve to speed up the evaporation and cool down the material, the organic solvent and water in the liquid material start to evaporate continuously, and flow into the liquid receiver for recycling after condensation, and the non-condensable gas is pumped away with the vacuum. Easy to clean, can be heated cycle cleaning, can also open the upper and lower cover of the heater and evaporation chamber for manual cleaning.


2. Process flow
This device is a high efficiency and energy-saving evaporation and
concentration equipment of external circulation, which is a fluid series unit designed by scientific calculation, such as heater, evaporation separator, condenser, liquid collector and functional pump.
The steam pipeline is connected to the single-effect heater, the vacuum system pipeline is connected to the separation chamber, and the material pipeline is installed, which means that the basic conditions for operation are available.
Solvent solution is evenly dispersed across all tubes. lt clings evenly to the inside of the tubes as it passes down.
Heating media, such as hot water or steam, is circulated through the shell side of the heat exchanger.
The walls of the tubes conduct heat energy evenly from the heating media into the process fluid which begins to vaporize as it heats. The solvent vapor accelerates down the tube along with the remaining liquid solution. The liquid is collected in the bottom of the system, while the vapor phase is sent to a condenser.
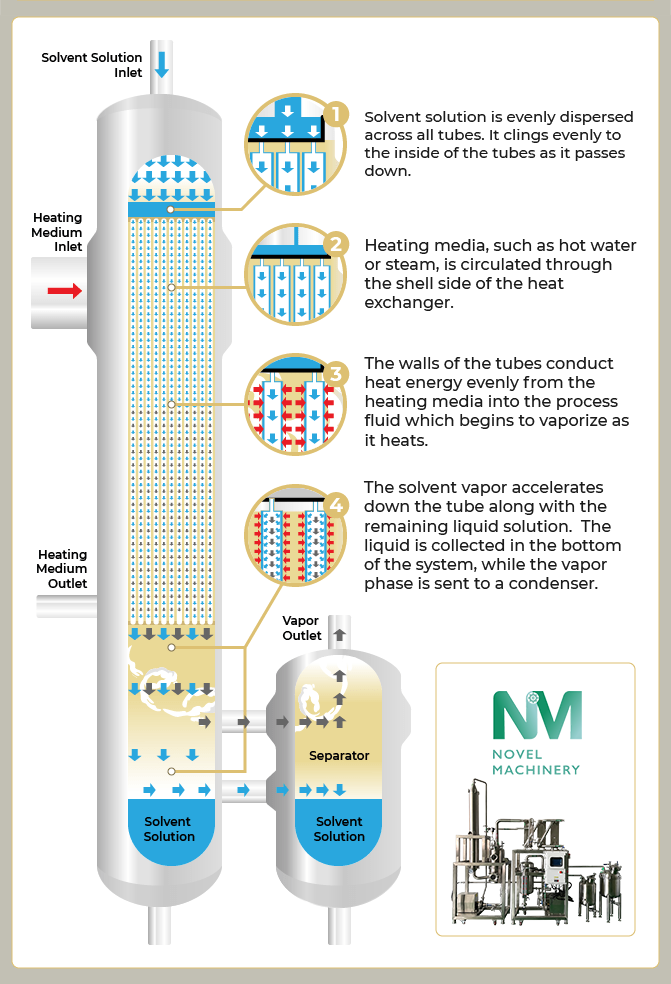
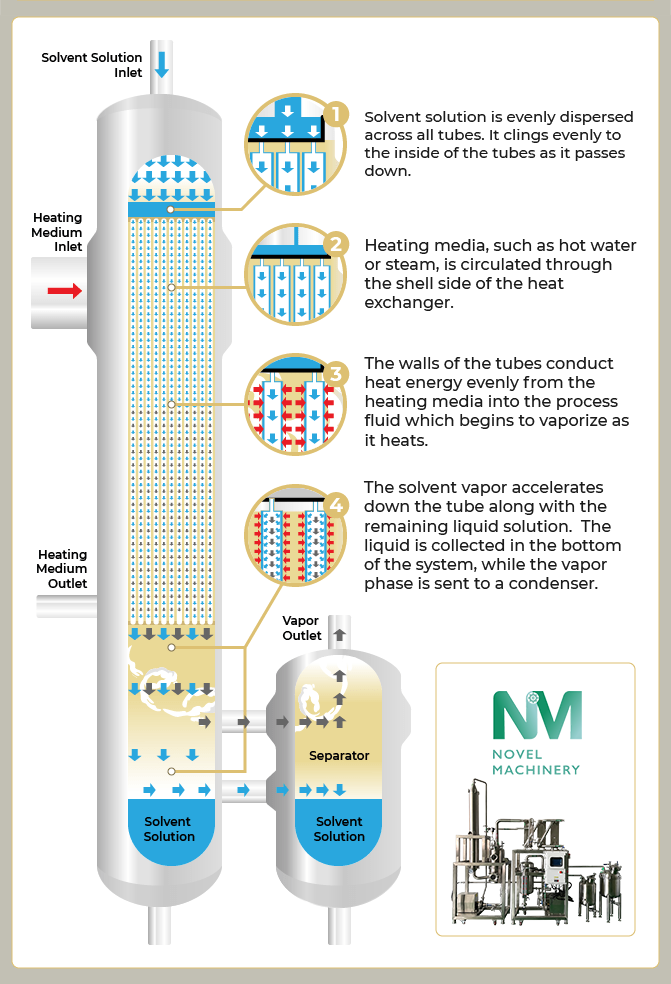
What is the material – what is added to the falling film evaporator?
Of course is the need to contain CBD liquid, we all know that CBD originated from hemp, the first need to use the centrifuge, the hemp leaves and alcohol together into the centrifuge, through the centrifuge centrifugal extraction, the hemp within the material, extracted into the material, this time the material not only contains CBD also contains THC and alcohol and other various impurities.
The material will be added to the falling film evaporator, we through the falling film evaporator gas, liquid separation, the material in the lower boiling point of ethanol gasification, to achieve the results of the elimination of ethanol.


3. Equipment Introduction
1.Evaporator
2.Oil-air Separator
3.Plate Head Exchanger (Preheater)
4/5.Plate Head Exchanger (Condenser)
6.Storage Tank
7. Control Cabinet(Anti-explosion)
8.Negative Pressure Discharging Pump (Anti-explosion)
9.centrifugual Discharging Pump(Anti-explosion)
+Water Ring Vacuum Pump


4, The operating procedures
1 Work before starting the machine
1) First check whether the equipment is clean and tidy.
2) Check whether the valves of the equipment are in the correct opening and closing position.
2 Start up the machine
1) Open the vacuum valve (pump) and wait for the vacuum to rise above -0.04, slowly open the feed valve, through the hose, the material will be sucked into the pipe. When the liquid level reaches 1/2 position of the lower sight glass of the evaporator, close the feed valve first.


2) Open the condensate bypass valve at the bottom of the heater, then slowly open the steam valve, and close the bypass valve after emptying the residual condensate in the shell process.
3) will open the heater steam to adjust the required pressure. Material forced circulation heating, in the spray into the evaporation chamber evaporation, vapor by vacuum extraction.
4) Open the condenser inlet valve and outlet valve, which can be moderately adjusted according to the evaporation capacity.
3 Normal operation
1) Depending on the liquid level of the material inside the condenser, carefully adjust the opening degree of the feed valve, and control the flow to keep the liquid level of the material inside the evaporator in the designated visible position of the evaporator, so that evaporation can be carried out normally.
2) The condensate is discharged by the water evacuator itself, and the bypass valve discharges non-condensable gas or air every 1~2 hours or so.
3) When the liquid collector glass tube level meter shows that the liquid is full, turn on the liquid discharge pump. Keep the backflow valve open 1/5 and the drain valve open 1/4.
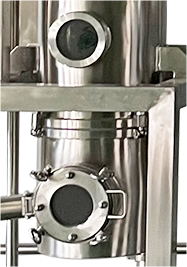
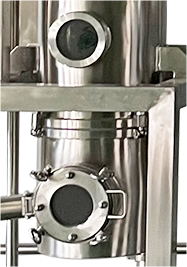
4 Paste collection operation
1) After reaching the required specific gravity (or solid content), close the feed valve.
2) Close the steam valve, vacuum valve and open the evaporator vacuum valve, open the discharge valve after atmospheric pressure while hot, and close the discharge valve after all the materials are in the storage tank. Immediately after discharging, stop and clean (or start to re-feed), so as not to reduce the liquidity of some materials after cooling or freezing.
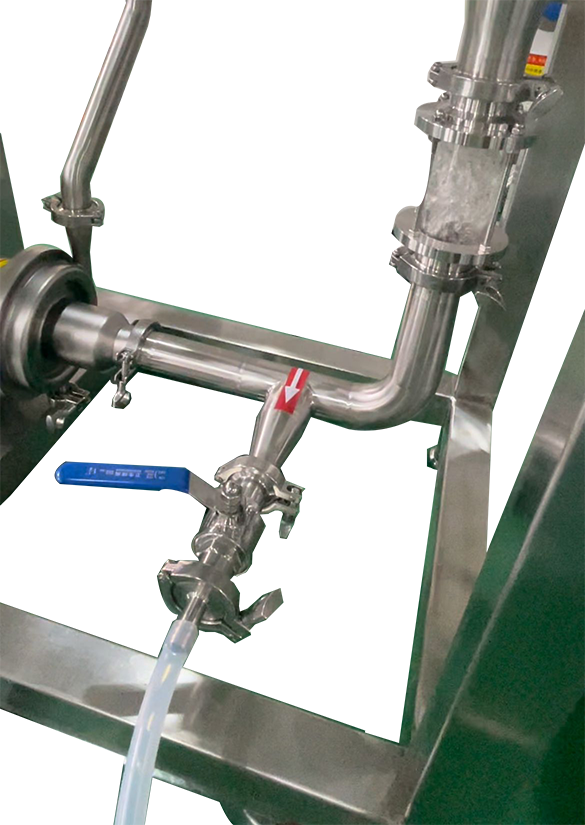
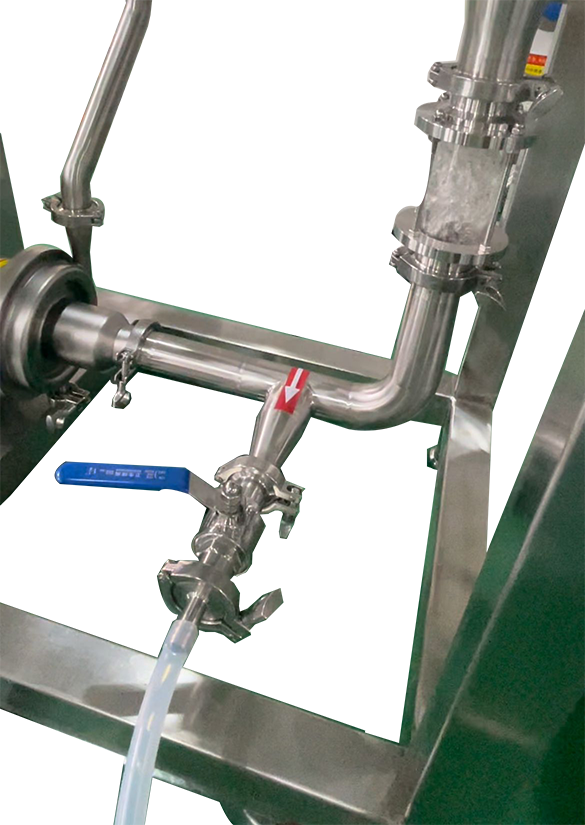
5 Stop operation
1) close the steam valve to stop the steam supply.
2) close the vacuum valve (or stop the vacuum pump operation).
3) open the evaporator venting valve, so that the equipment from the negative vacuum pressure to atmospheric pressure.
4) Open the liquid collector venting valve and drain the liquid, and drain the collected liquid.
The falling film evaporator is equipped with continuous ethanol recovery tank and vacuum tank 50-350L/hr evaporation rate available
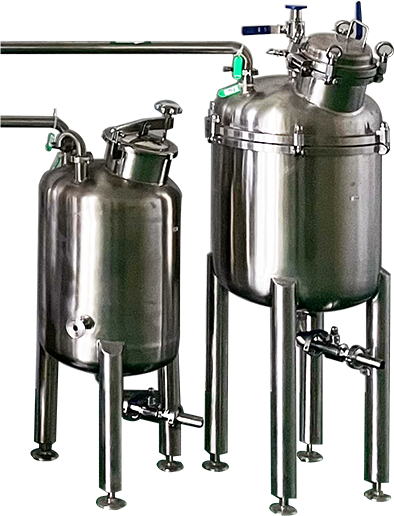
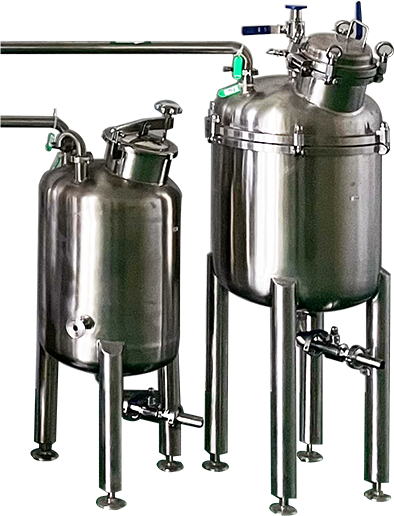
5. Provide turnkey solutions


01 High efficiency evaporation
The top of the evaporator is designed with spray cloth, so that the material is fully distributed on the surface of the tube heat exchanger. Greatly improve the heat.
Exchange and evaporation efficiency, reduce.
Residence time of materials and the risk of denaturation of heat-sensitive compounds, recovering 50-350L of ethanol per hour.
02
Innovative gas-liquid separation design.
The evaporation chamber adopts spiral design to accelerate liquid precipitation, quickly achieve gas-liquid separation, recover better solvent appearance and reduce material loss.
03
Secondary evaporation and complete focus
The negative pressure discharge pump can freely switch the circulation discharge mode to achieve secondary evaporation for the materials not completely evaporated. For high viscosity materials, it has better discharge capacity than ordinary explosion-proof centrifugal pump.
04 316LS welded high efficiency
Heat exchanger
Three sets of S316L welded heat exchangers are used to condense steam for efficient heat exchange and environmental protection.
The first heat exchanger preheats the material to realize energy saving and emission reduction.


05
The whole machine is explosion-proof and modular design
The pipeline and evaporation chamber are equipped with sight glass, which can see the evaporation process in real time. The whole machine adopts explosion-proof design, compact structure, easy to assemble and move.
6. Special features
Best product quality.
Due to its gentle evaporation (mainly under vacuum) and very short residence time in the falling film evaporator.
High energy efficiency.
Due to its multi-effect arrangement or heating by thermal or mechanical vapor recompression.
Utilization of recovered waste heat.
Due to the flexible design of the heating side, the evaporator can be heated by exhaust gas or hot water.
Simple process control and automation.
Due to its low liquid content, it responds quickly to changes in energy supply, vacuum, feed volume, concentration, etc.
Flexible operation. Quick start-up and easy changeover from operation to cleaning, as well as simple product changes.
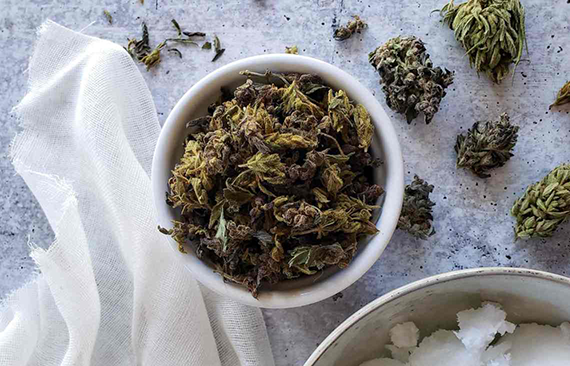
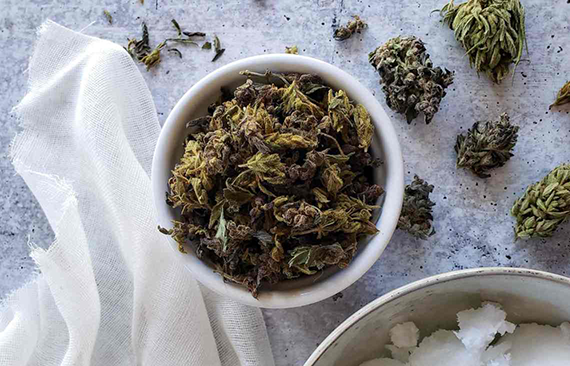
7.Notes
1) Feeding: When the vacuum level in the device reaches 380mmHg, open the feeding valve, close the feeding valve when the liquid level of the material rises to the evaporator liquid level sight glass and open the circulating pump, and open the steam inlet valve of the heater when the vacuum level of the device reaches 600mmHg.
(2) into the steam: the use of this device to concentrate materials should not be in the heater material (or water) does not reach the appropriate level and not open the cycle of materials to open the heating steam valve, which will make the inner wall of the heating tube overheating and material coking so as to affect the normal operation of the device; at the same time should pay attention to the pressure of heating steam, so that it does not exceed 0.09Mpa, to avoid boiling and the phenomenon of running material, steam safety valve can be set at 0.1MPa.
3) Discharge: depending on the liquid level rise speed of the collector to control the discharge speed equal to it, can also be slightly greater than its liquid level rise speed, has been maintained in the state of playing out can also (low liquid level when the top does not open the check valve to maintain the cycle), when the evaporation is completed to close the vacuum to restore atmospheric pressure, and finally open the bottom discharge valve, drain the valve back to the normal operating position.
4) Discharge material: When the operation has been carried out for a period of time, the degree of concentration of the material can be observed from the liquid level sight glass, or the proportion of concentration can be measured by taking samples, and when the concentration is close to the requirement, the feeding will be stopped, at this time, the steam valve and vacuum valve will be closed immediately, the evaporator venting valve will be opened to return to normal pressure, and the concentrated material will be discharged by opening the discharge valve of each effect while it is still hot.
Cleaning: After the material is discharged, the same batch of material can continue to be concentrated, and the operation steps are the same as above, if the evaporation and concentration operation is no longer carried out, the cleaning should be carried out immediately. Cleaning can be carried out alternately with detergent and hot water according to different requirements, and finally soaked with water, which is added to the high level of the liquid level sight glass, and the water will be released before the next operation.
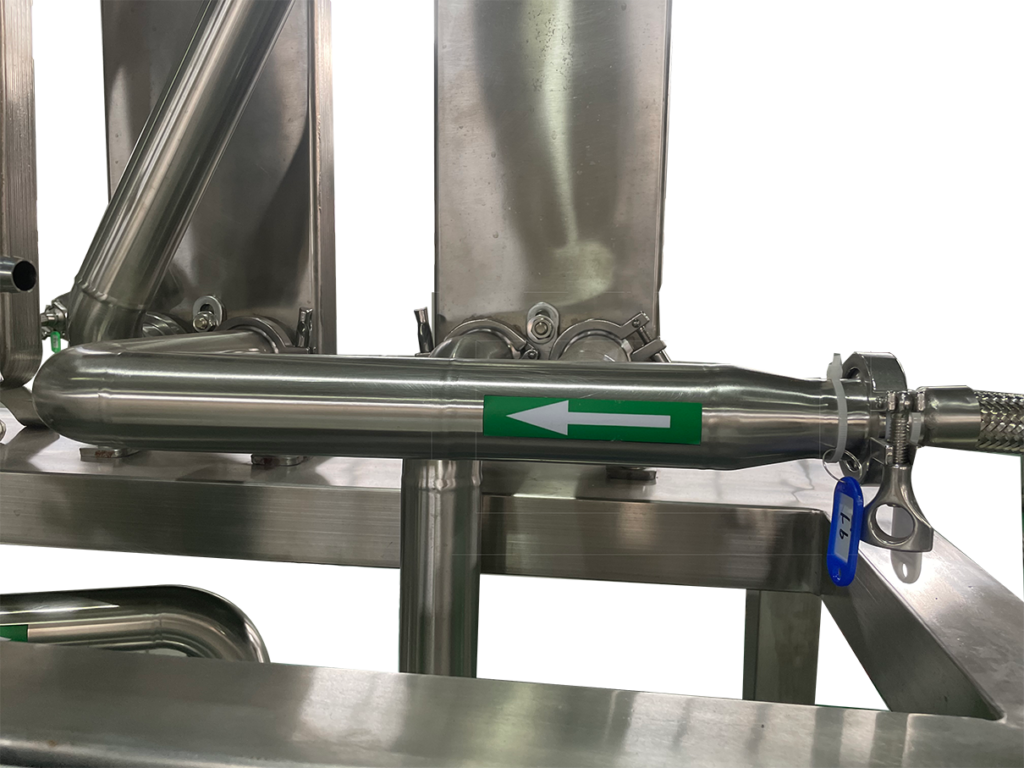
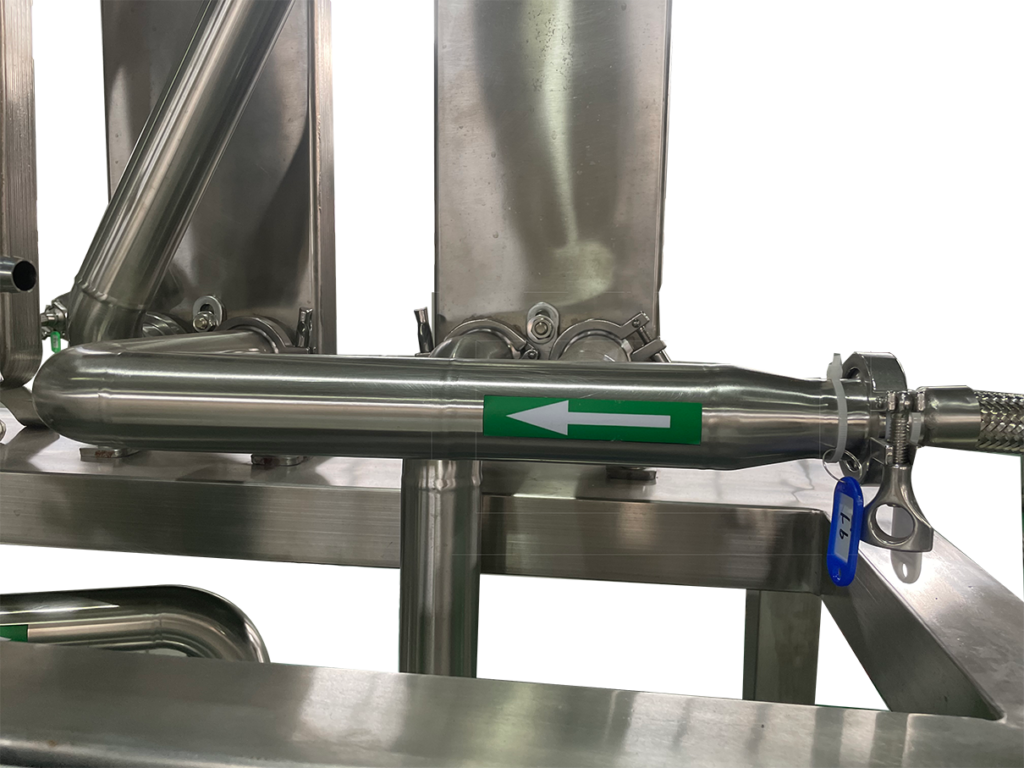
8, The equipment cleaning
(1) normal operation, the heater can be ten days to clear brush once. When the heating steam pressure is found to have a significant increase in the heat exchanger tube has formed scale, affecting heat transfer, it should be stopped to open the top cover of the heater, with a round steel brush to remove the scale in the heating tube or high-pressure water gun rinse; evaporation chamber can also be opened to brush and wash the inner wall.
(2) cleaning variety: boil with 1% caustic soda solution for half an hour and then use round brush to clean the heat exchanger tube, and then clean with water. Open the hand hole of the evaporator with hot water to brush and wash the evaporation chamber.
3) Stop cleaning: out of the appropriate amount of water steaming for about half an hour, release the sewage, and then clean water, to be clean and close the water inlet valve to drain the water.


9. Why choose cold ethanol for cannabis extraction?
Ethanol is an ideal solvent for plant oil extraction for a number of reasons, but the most influential reasons for choosing cold ethanol as a solvent when it comes to cannabis or hemp extraction are
1. its chemical structure allows it to extract or dissolve most polar and non-polar molecules. In the case of cannabis, this is ideal for “full spectrum” products. This ability can also be controlled by the solvent temperature. 2.
Because it exists as a non-viscous liquid at ambient temperature and pressure (unlike other popular solvents such as CO 2 and hydrocarbons), it can extract molecules quickly and easily. For example, the processing time is much faster compared to hydrocarbons and CO 2.
The basics of the cold ethanol extraction process are very easy to understand and are very similar to the way other solvents are used. Almost all solvent extraction of cannabis or marijuana consists of three main steps, usually accompanied by a few other minor processes depending on your SOP and desired end product goal: extraction, evaporation and distillation.
In the second step of evaporation, we take the solution obtained in the first step (a combination of solvent and our target compound THC/CBD, etc.), then apply vacuum and heat. This causes the solvent to boil, leaving the desired compound in crude form, which is also called crude oil – with an average cannabinoid potency of between 40-60%. Finally, the third step of distillation is a process very similar to evaporation, in which we apply a deeper vacuum and add more heat. However, this time we try to target and “boil” the cannabinoids themselves (as opposed to targeting the solvent in our evaporation process) to further refine and separate them. This stage usually yields 85-95% of the distillate.




10, solvent evaporation: rotary evaporation and falling film evaporation
After saturating the ethanol solvent with cannabinoids, the next step is to separate the solvent from the tincture by evaporation. There are two main methods to perform this step.
1. Roto Evaporation is a popular tool for solvent removal as it is easily scalable to startup and large scale extraction labs. It works by removing the solvent under vacuum through a rotating temperature-controlled vessel that is partially submerged in a water bath. A spherical distillation flask is filled to about half its volume with a cannabinoid-rich tincture. The water is heated to approximately 30-40°C and the condenser temperature is set at -10°C to 0°C. The distillation flask is then rotated at 150-200 rpm to produce a film on the inner surface of the glass cylinder for solvent evaporation.
In contrast, a falling film evaporation machine works in a similar manner, but is more efficient than rotary evaporation. Falling film evaporation maintains a high evaporation rate, significantly increasing the throughput of crude oil production without the need for multiple large rotary evaporator systems. This saves time and lab space in extraction facilities. Less exposure to high heat, along with faster processing speeds, make the CBD series an important part of the processing line. The short residence time is ideal for heat sensitive plant compounds, reducing the risk of burning oil.
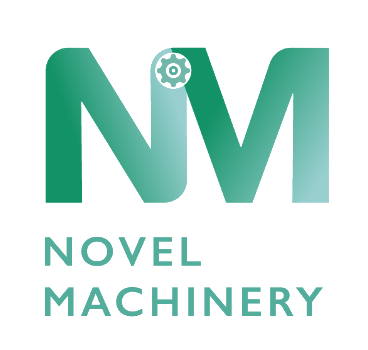
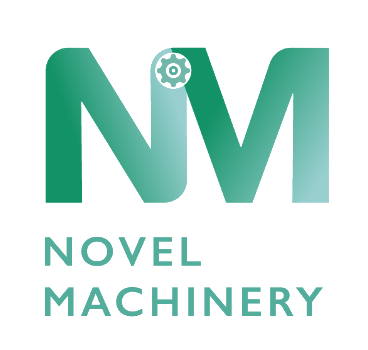
For more details, please contact NOVEL machinery!