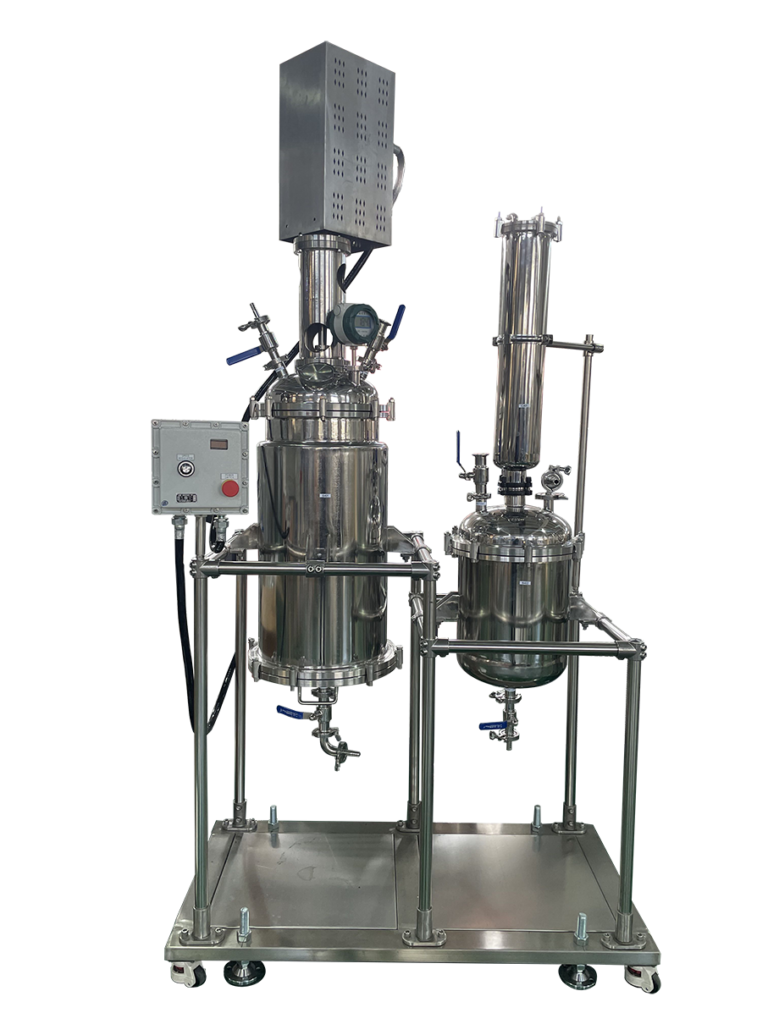
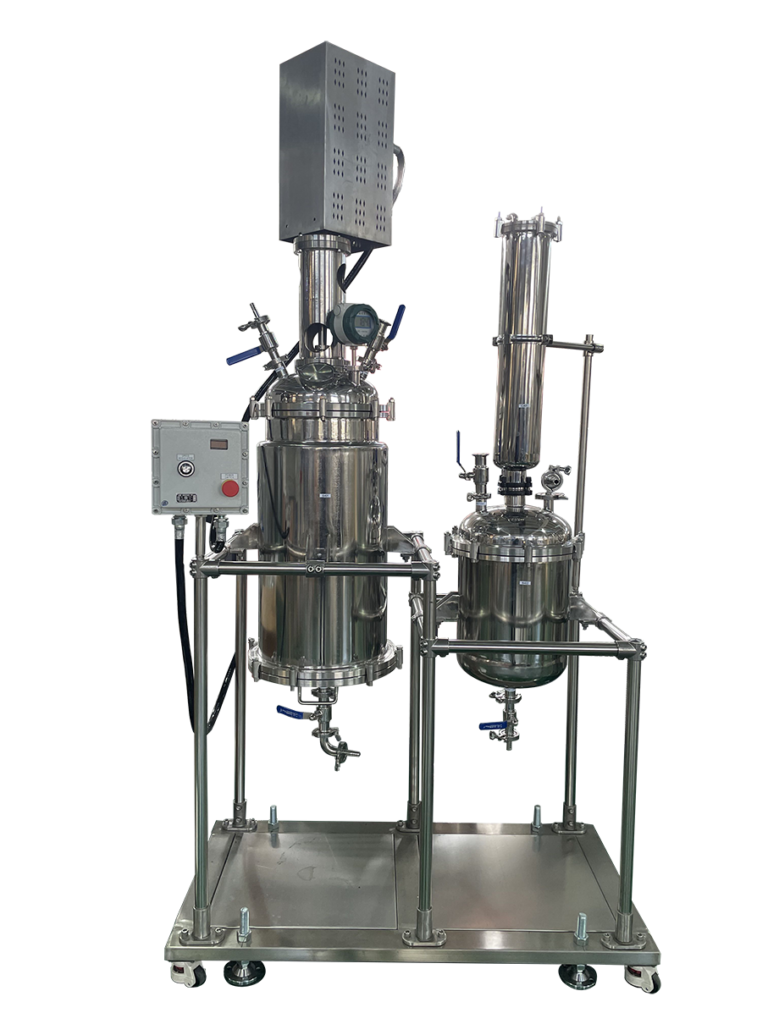
First, product overview
Crystallization tanks are mainly used for crystallization of liquid materials in pharmaceutical, food, chemical, biological products and other industries (by physical methods such as cooling to make a solution in a saturated solution reach an oversaturated state to form grain precipitation), separation. The equipment where the contact with the liquid is made of 316L stainless steel, with non-toxic, non-falling, good corrosion resistance and so on, not only can make the pharmaceutical, food quality is guaranteed, but also the long service life of the equipment.
Second, safety precautions
Danger – When used incorrectly, it can cause danger and may result in personal death.
Note – Misuse may result in minor personal injury and equipment damage.
1, Acceptance
When the product is received, do not install it if it is found to be seriously damaged or bumpy. May affect product performance.
2, Installation
Should be installed on a ground or platform of sufficient strength. Heavy equipment load, may cause ground pressure, equipment tilt
Collapse. Each connector of the device should be secured. There is a risk of affecting the operation of the equipment. Do not remove the instrumented parts at will, if the lifting may damage the instrument, please follow the specifications or instructions to remove the instrument.
Damage to the instrumentation may occur. Personnel are prohibited from climbing equipment. Risk of falling or damaging equipment.
When handling fixing, a professionally qualified equipment engineer should guide the installation on site. During installation, it is necessary to lift, move, there is a risk of injury and affect the operation of the equipment. When lifting equipment, please choose the appropriate lifting tool according to the weight of the product, to prevent the lifting tool can not bear the weight of the equipment. There is a risk of injury or injury or damage from equipment falling. The ground end must be reliably grounded. Risk of electric shock and fire.Equipment that requires power-up should be wired by a professionally qualified electrical engineer. Risk of electric shock and fire.
3, Trial run
Do not overpressure overshoot during operation. There is a risk of explosion. The storage of flammable and explosive liquids and gases should be equipped with flame retardants and open flames shall be prohibited. There is a risk of explosion.
When storing strong acids, alkalis, and corrosive articles, staff should wear appropriate labor protection supplies. Risk of burns.
When storing high-temperature, very low-temperature items, staff should also wear appropriate labor protection supplies. Risk of burns.
The instrument should operate within the temperature and humidity range required by the parameters. There is a risk of affecting the accuracy of the instrument. Do not use wet hand knobs and operating switches. Risk of electric shock. When the device is running, reduce exposure to the mirror and prevent poor guidance in the mirror installation Causing pressure to break, harming personal safety.
4, Maintenance and maintenance
Do not self-modify .There is a risk of changing parameters such as operating pressure on the equipment. Non-professionals, do not carry out maintenance and inspection. Risk of damage to equipment and injury
When removal and maintenance is required, always look for Trained or supplier-maintained by the relevant qualifications. Can cause damage to the device.


Third, the structure overview
Stainless steel crystal kettle is mainly composed of tank body and accessories.
The body is mainly composed of the barrel, legs, upper and lower head, jacket and insulation layer. Crystal tank cylinder cylindrical, upper and lower cap is standard oval or butterfly head, inner bile and material contact material are 316 stainless steel, jacket, outsourcing not contact material material are 304 stainless steel.
Insulation materials are mostly polyurethane or rock wool cotton (in this project due to the low temperature of the use of low temperature aerogel, the use of temperature -60 to 65 , 7 5mm thick.
Accessories mainly include sanitary manholes, stainless steel blind plates, fluid import and export and other process pipe mouths,
CIP cleaning port, mixing system and other options such as thermometers, cleaning balls, sanitary valves, etc.


Fourth, specifications and technical parameters
Five,Product performance
This product has superior performance, mainly in the following aspects:
1, operating performance
The accessories of the crystallizing kettle (e.g. cleaning ball, import and export, manhole, ball valve, mixing system, etc.) are reasonably distributed, both for observation and operation. Often connected with the automation control system, with automated instrumentation, can directly read the liquid temperature, volume, and pressure in the tank, so that the control of process parameters more precise, greatly improve product quality, reduce labor strength.
2, health performance
Crystallization Kettle for the upper part of the oval head, the following oval head form; Each pipe port weld is arc-throwing, ensuring a smooth transition of its corner part with an R arc, and ensuring that the inner surface roughness Ra ≤ 0.45μm This avoids product residue and meets the crystalline tank requirements.


Six, control system
Crystallization Kettle Control Part is mainly a mixing control system.
The mixing system is divided into up and down according to the installation bit. On the stirring is often mechanical stirring (this equipment using mechanical stirring).
Mechanical stirring: the mixing motor is installed on top of the tank, the mixing shaft consists of the upper half shaft and the lower shaft, wherein the upper shaft and the tank are sealed with good sealing performance, long service life of mechanical seal, the lower shaft is connected by flanges and the upper half shaft, stirring blades are welded on the lower stirring shaft.
Speed control has manual mechanical speed control and variable speed control two. Mechanical speed control is achieved by turning the gearbox speed-controlling handwheel; Variable frequency speed control by changing the power supply frequency to achieve speed control; See Speed Cookbook. Or fixed speed (fixed speed for this device).
Magnetic stirring: the drive motor is installed in the bottom of the tank, the motor shaft is directly connected with the internal magnetic steel, the external magnetic steel is molded with the stirring blade in one, the internal and external magnetic steel is completely isolated from the sleeve, not in direct contact. When the motor rotates, the internal magnetic steel drives the external magnetic steel rotation by magnetic effect, thus achieving the stirring effect.
Seven, installation and commissioning
When the device arrives at the user’s site, the user should carry out an out-of-the-box inspection. When unpacking the shipping party and the demand side should be present at the same time, in accordance with the invoice to check the number of equipment, equipment models, and spare parts list, found that there is any non-compliance with the invoice, timely contact manufacturers for advice. Check the quantity model should be checked on the appearance of the equipment, should be no scratches, bumps and other phenomena, if there should be timely contact manufacturers. Check the equipment connection part is loose, if loose, the general parts can be self-tightening, key components should contact the manufacturer.
Crystallization of the outer surface of the kettle has been fine polishing treatment, therefore, in the handling, lifting, to pay special attention to protection, not collision, if you need to roll over, be sure to lay rubber plate and other soft materials on the ground.
When lifting, do not directly use steel cables, can be used to lift the surface with a rope or with cloth, cotton yarn and other protective surface. You should also note the following:
1, according to the plant floor plan installed in the established location.
2, in strict accordance with the process of installation.
3, do not change the installation location and pipe diameter size at will.
After being in place as required by the process, connect the corresponding pipes by reference to the identification of each pipe (note: avoid pipeline crossover and ensure non-interference in valve operation) and color and choreograph according to the corresponding regulations umber.
After installation, check the convenience, reasonableness, safety, and Compliance with process and design requirements is subject to strict installation quality confirmation in accordance with GMP or FDA or other standards. Then the temperature gauge, pressure gauge and other instruments of the crystallization tank are corrected and confirmed, the volumetric check, the air tightness inspection of the equipment and related pipes, the self-opening performance test of the safety valve (if any) and so on (i.e. the operation confirmation). After confirming the qualification, according to the process conditions for water test and medium test drive simulation operation, complete the operation performance confirmation;
1, Flanges interface installation notes:
To ensure that the flanges are horizontal or vertical, the deviation does not exceed 1% of the flange’s outer diameter and is not greater than 3mm;
- Before installing the flange, the gasket should be properly secured to prevent the gasket from slipping during installation;
- The bolts used for the installation of flanges shall be in a uniform direction, and for pressure vessels, they shall be selected in accordance with the specifications or standards recommended by the manufacturer, and shall not be arbitrarily reduced;
- Diagonal pretension should be used when tightening bolts to prevent uneven flange installation and leakage dew.
2, Quick-loading connector installation precautions:
Connections should be made using fast fittings of the same specification, joints of different nominal diameters should not be used for connection, if connections of different tube diameters must be connected, connections should be made using eccentric fast fittings to avoid mutations and dead ends in the pipes;
When installing fast fittings, should ensure that the gasket installation is secure, especially when horizontal installation, there should be measures to prevent the gasket slipping, the installation process to ensure that the two quick-loading connector alignment is not misplaced, if necessary, you can use tools to tighten the clamps.
3, Threaded connector installation notes: The sealing form of threaded joints is generally divided into end face seal and threaded face seal, so To make threads sealed with end faces, check that the sealing surfaces are flat before installation, the installation process should ensure that the thread tight, to avoid the gasket is not compacted leading to leakage;
4, Threads sealed with thread surfaces are generally tube threads, should use a sufficient amount of raw material belts in the direction of thread winding around the outer thread, and at least 2/3 of the effective length of the outer thread into the inner thread, to avoid internal and external thread seal is not strict, resulting in leakage.
5, valve installation precautions:
Before installing the valve should ensure that there are no granular impurities in the pipe, to prevent the valve after installation of impurities into the valve, resulting in the valve closed not strict;
- Check the valve switch situation, the stem and valve body should be switched freely, if necessary, the valve door can be individually sealed and strength pressure test, after passing the test in accordance with the flange or fast-loading or threaded installation precautions to install the valve;
6, the installation of each instrument note:
- According to the user needs crystal can generally be equipped with pressure gauges, thermometers and other instruments, this type of instrument is mostly fragile, in the installation process should be lightly placed, strictly prohibited brutal installation or removal, collision, due to collision and other adverse reasons caused by inaccurate instrument display and its consequences, we are not responsible.


Eight, equipment operation
1, Preparation
- Read the technical documentation provided at random carefully before use.
- Check that the crystalline tank has been cleaned and disinfected for use.
- Check that the connection tubes are sealed in good condition and that the valves are open normally.
- Check that the control sections (including electrical, instrumentation) are OK.
- Check the circuit connection of each pump to ensure that the motor circuit connection of each pump is normal, to prevent inversion, lack of phase and other failures.
- Check the installation status of each instrument, ensure that each instrument is installed in accordance with the specifications, the quantity process meets the production requirements, and each instrument is used within the validity period of the calibration.
- Check the installation status of each valve to ensure that the valves are installed in accordance with the specifications.
- Check the air tightness of the system, to ensure that the pipes do not run and drip and other phenomena;
- Check that safety components such as safety valves have been installed in accordance with the specifications; Check that the valve at the respirator is open.
2, Normal production
- Open the feed valve and material delivery pump power feed, observe the level height, to the appropriate amount after closing the feed valve and the delivery pump power supply.
- If heating or cooling is required, open jacket steam or frozen water inlet and outlet, heat or cool the liquid through the jacket, observe the temperature gauge, and close the heat exchange
- System import and export valve after reaching the temperature required by the process.
- In operation, always pay attention to the heat exchange system temperature gauge, pressure gauge changes, avoid the phenomenon of overpressure overshoot.
- When the discharge is required, open the discharge valve and deliver it through the pump to each point of use.
- After stirring in due course, turn off the agitator; Close the media inlet first, then close the media outlet.
- Open the discharge valve, discharge out.
- When the discharge is complete, close the discharge valve.
3, The end of production
- Turn off the total power supply to the distribution box.
- The crystalline tank shall be cleaned and disinfected according to the maintenance terms of the equipment.
(This operating procedure is for informational purposes only, depending on the process of each user unit).
Nine, clean equipment
1, cleaning method
The crystalline tanks and connecting pipes need to be thoroughly cleaned after work or before changing the varieties every day.
A,tank cleaning:
- Open the CIP cleaning system, open the valve with stirring CIP inlet and tank bottom drain, according to the CIP cleaning procedure, automatic cleaning inside.
- Close the drain valve, fill the container with half the volume of hot water, and drain the water after 10 minutes of turning the agitator.
- Rinse the inner wall of the tank with hot water.
- Add 1/3 volume of distilled water (pure water) to the tank, close the drain valve, turn the agitator for 10 minutes, take a sample of the water and drain the water.
- Close all valves, check the cleaning effect, confirm that the water sample is qualified, complete the cleaning in the tank.
B, outside the tank cleaning:
- Depending on the cleaning of the outside surface of the tank, wash clean with gauze from time to time.
- Do not rinse the meter, gearbox site with water.
2, Disinfection method
After cleaning the crystalline tank, useless vapor sterilization method,
should be used other sterilization methods such as acid and alkali washing.


Ten, equipment maintenance
1, After each production cycle, the equipment should be thoroughly cleaned.
2, According to the production frequency, regular inspection of equipment, whether there are loose screws, whether there is gasket damage, whether there is leakage, and whether there are other factors that may affect product quality, and timely check records.
3, Regularly check the operation of the agitator and mechanical seal, scraper wear, found abnormal noise, wear and other conditions should be repaired in a timely manner.
4, Agitator at least every six months to check, reducer lubricant should be immediately replenished, semi-annual oil change.
5, Every six months to the equipment barrel body range to carry out a test leak test.
6, Long-term need not clean the equipment, and dry storage. Before re-opening, a thorough inspection of the equipment is required before it can be put into production.
7, Daily to do a good job of equipment use diary, hould include operation, maintenance and other conditions.
8, After each repair should be the operation of the equipment to confirm, after the overhaul to re-examine the equipment proof.
If there is steam in the crystalline tank, the pressure gauge and safety valve must be installed on the steam inlet line.And in the installation and use of regular checks, in the event of a fault, to immediately adjust or repair
9, The pressure setting of the safety valve, according to the user’s own needs of pressure, self-adjustment, but do not exceed the prescribed work pressure.
10,When the crystalline tank during the use, it is strictly prohibited to open the human hole and each connecting tube card.
11, Ccrystalline tank pipe connection for the card plate structure, such as the use of liquid leakage running gas phenomenon, should be replaced in a timely manner.
12, Strict for the storage tank corrosion of the media environment. When storing liquids such as acid and alkali, the reservoir should be passivated, chlorine ions are extremely destructive to stainless steel, and adequate attention should be paid to the pitting of equipment (the jacket circulating medium chlorine ions should be prevented from exceeding the standard).
Eleven, equipment troubleshooting
Symptom | Possible causes of the failure | Processing methods |
1, The heat exchange effect is not good。 | Faulty egress connection. | Connect the right way. |
The jacket is clogged. | Unblock. | |
2. The valve leaks. | The gasket is damaged. | Replace with a new gasket. |
The valve is damaged. | Replace the valve with a new one. | |
3. The instrument and meter display is inaccurate or not displayed. | The meter is damaged. | Replace with a new one. |
Connection error. | Reconnect in the correct way. | |
4, The tank has a leak. | The tank is damaged. | Make patches. |
5. The tank is rusty. | The outside environment is not suitable. | After rust removal, store in suitable conditions. |
Scratches on the surface. | Reprocessed and locally passivated. | |
6. The insulation layer is partially over-hot | The jacket is broken | Make patches |
7. Water infiltration of the insulation layer and water leakage of the jacket. | Insulation, jacketing, tank leakage。 | Find leaks to patch. |
Transport and storage
There are a few things users should pay attention to when transporting and storing equipment:
1, the outer surface of the tank has been fine polishing treatment, so in the transport process, special attention should be paid to protection,
The outer surface should be packed, do not collide, if you need to roll over, be sure to lay rubber plate and other soft materials on the ground.
2, if you need to lift, do not directly use steel cables, can be used to lift rope or with cloth, cotton yarn and other protective surface.
3, equipment long-term use should be dry storage.
4, Equipment should not be stored in the air containing chlorine ions for a long time.
5, Avoid rain and direct sunlight.
6, prohibit violent loading and unloading.
Twelve, the appearance of the device and control button description
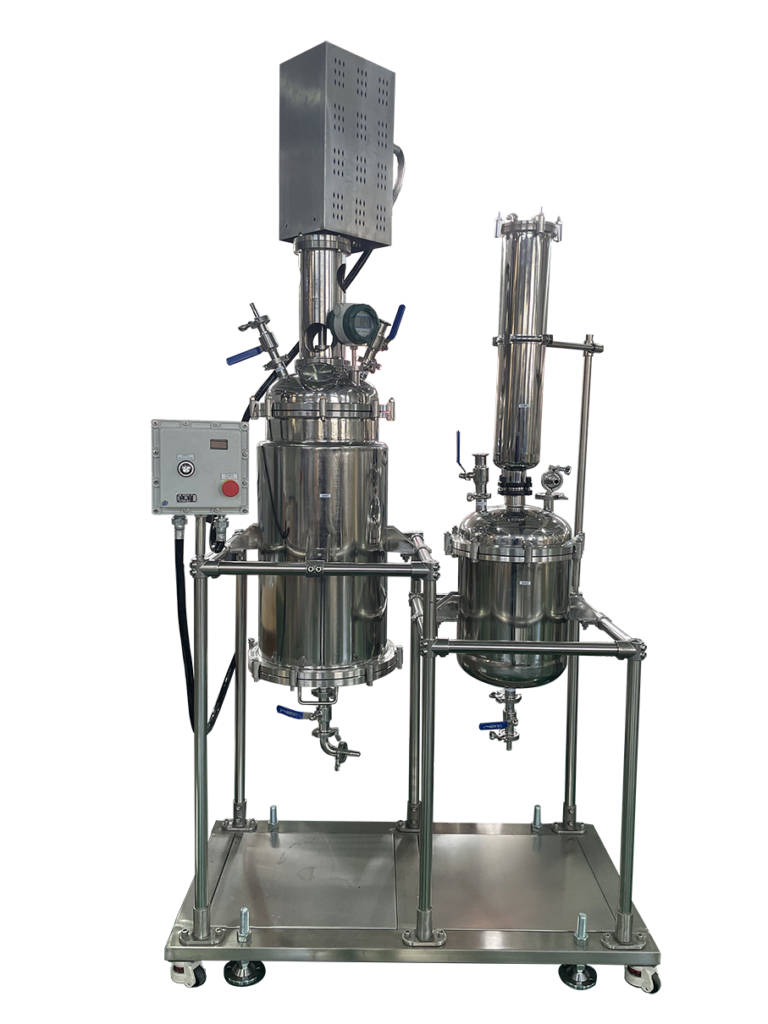
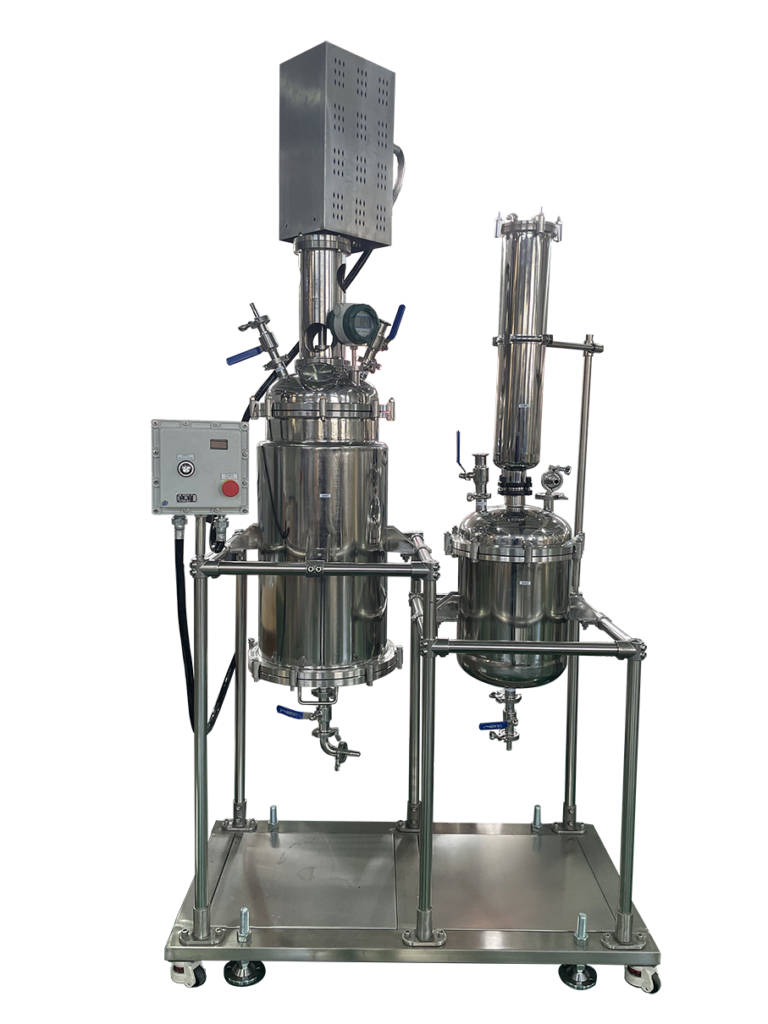
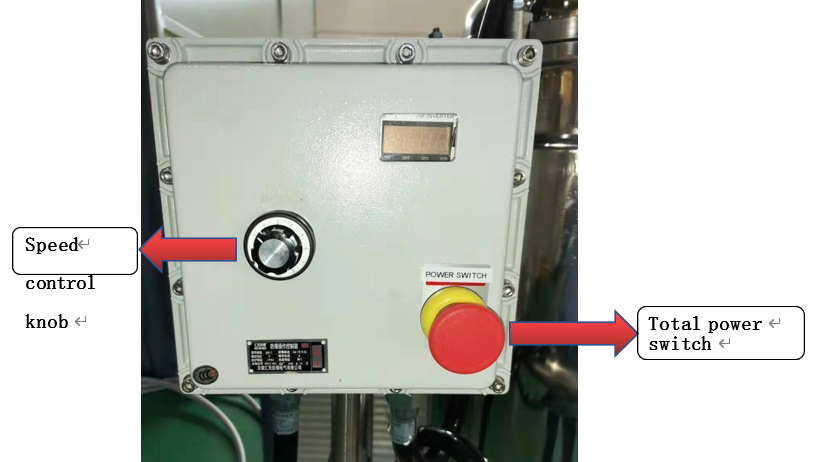
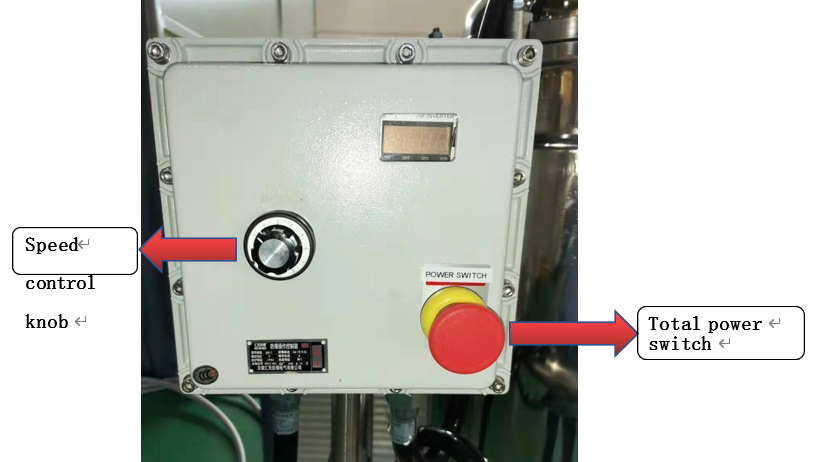


Thirteen,The working principle of crystallization
The crystallization process must reach supersaturation of the solution to crystallize, stainless steel crystallization tank design needs to meet this condition, and to create conditions for the crystallization process and crystallization mode. Therefore, the crystallization process is the process of saturating the solution. According to the way to make the solution to supersaturation, crystallization methods can be broadly divided into several categories.
1. Evaporation crystallization
Evaporation of the solution at atmospheric or reduced pressure by heating, part of the solvent evaporates so that the solution is concentrated to supersaturation and thus precipitates crystals, this method is called evaporation crystallization. Evaporation crystallization is divided into three types: atmospheric pressure evaporation crystallization, reduced pressure evaporation crystallization and azeotropic decompression crystallization.
2. Cooling crystallization
The method of precipitating crystals by lowering the temperature so that the solution reaches supersaturation is the freezing crystallization method. This method is suitable for substances whose solubility decreases significantly with temperature. Cooling crystallization is a device that relies on lowering the temperature of the material to produce supersaturation and eventually cause the material to crystallize. At present, with stirring or external circulation kettle-type crystallizer is widely used, its cooling can be taken to jacket heat exchange or through the external heat exchanger to achieve; direct cooling junction products rely on the solution and cooling medium directly mixed refrigeration, cooling medium commonly used ethylene, Freon and other hydrocarbon inert liquid. Direct cooling crystallization has a variety of kettle-shaped, rotary, wet-wall tower type. This equipment is suitable for processing solubility with the temperature drop and significantly reduce the material system.
Cooling crystallization is further divided into internal circulation cooling type and external internal circulation cooling type crystallizer according to its cooling form. The cooling capacity required for the cooling crystallization process is provided by a jacket or an external heat exchanger. Internal circulation cooling crystallization has heat exchange between the coolant and the solvent through the jacket of the crystallizer. This equipment has a small heat exchanger volume due to the heat exchange area of the heat exchanger being limited by the crystallizer.
External circulation cooling crystallization whose coolant and solution exchange heat through a cooler outside the crystallizer. The heat exchange area of this equipment is not limited by the crystallizer, and the heat transfer coefficient is large and easy to achieve continuous operation. Cooling crystallization is the area where supersaturation is generated and the crystal growth area are two places of the crystallizer respectively. The crystals are fluidized and suspended in the circulating mother liquor, which provides better conditions for crystal growth and can produce crystals with large and uniform size.
The working principle of cooling crystallization: it adds a column cooler in the circulation pipeline, the mother liquor circulates upward through the column pipeline in one way, the thick material liquid is added before the circulation pump, mixed with the circulating mother liquor and then cooled together through the cooler to produce supersaturation, after which it enters the fluidized suspension in the crystallizer to produce crystals with large and uniform size. The product (crystals) suspension is led from the bottom of the crystallizer cone.
3. Heating crystallization method
Raising the temperature also enables some solutions to reach supersaturation and thus precipitate crystals. This method is suitable for substances whose solubility decreases significantly with the increase in temperature.
4. Reaction crystallization method
Adding certain chemicals or adjusting the PH to change the chemical composition and properties of the solute to make it change from a soluble state to an insoluble state, thus reaching supersaturation and precipitating crystals.
5. Salt crystallization method
This is a method of crystallization by adding another substance to reduce the solubility of a solute in a solution to achieve supersaturation. There are two kinds of salt crystallization methods.
1, adding a solute, called salting agent, so that another solute in solution to reduce the solubility of the solution to reach supersaturation.
2, add another solvent, so that the solute in solution then mixed solvent to reach supersaturation and crystallization out.
Our equipment uses cooling crystallization. Cooling crystallization relies on reducing the temperature of the material, thus causing the material to become supersaturated, and finally prompting the material to crystallize the equipment. At present, with stirring or external circulation kettle-type crystallizer is widely used, its cooling can be taken to jacket heat exchange or through the external heat exchanger to achieve; direct cooling crystallization relies on the solution and cooling medium directly mixed refrigeration, cooling medium commonly used ethylene, Freon and other hydrocarbon inert liquid. Direct cooling crystallization has a variety of kettle-shaped, rotary, wet-wall tower type. This equipment is suitable for processing solubility with the temperature drop and significantly reduce the material system.
(Depending on the user unit process)

