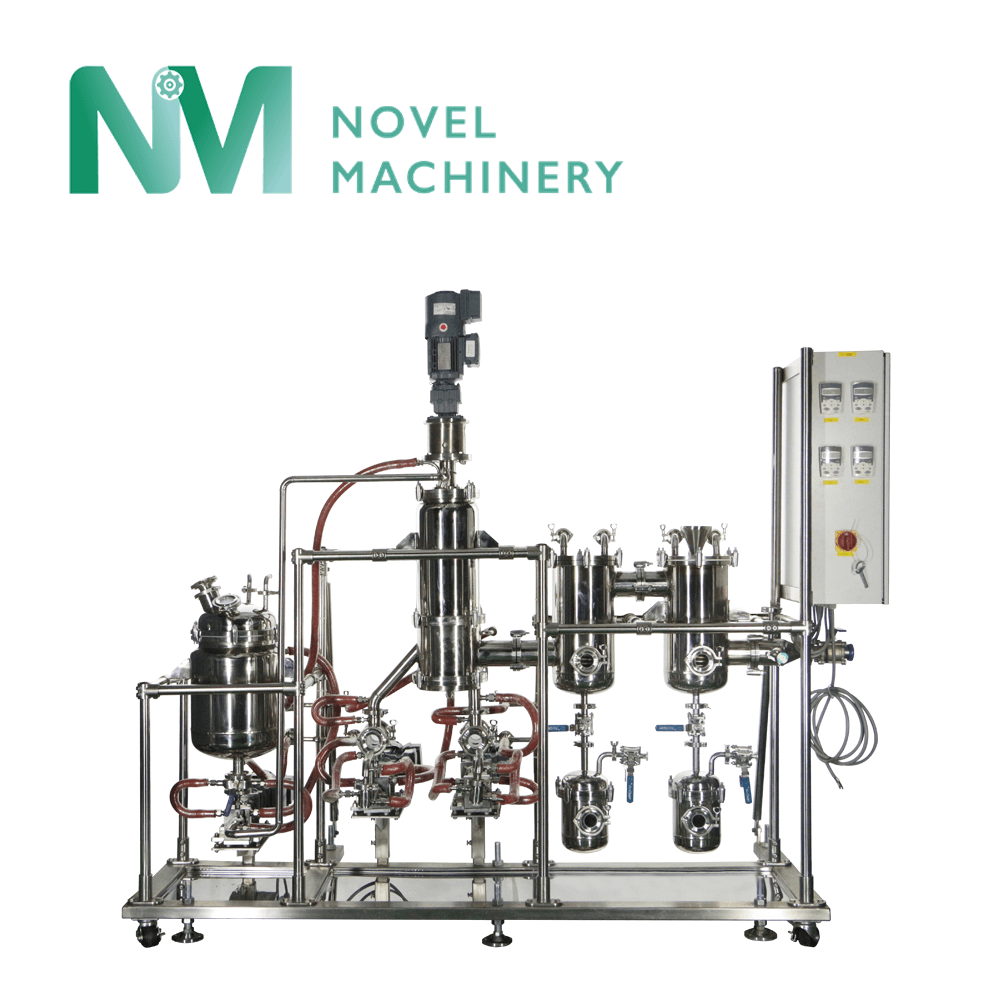
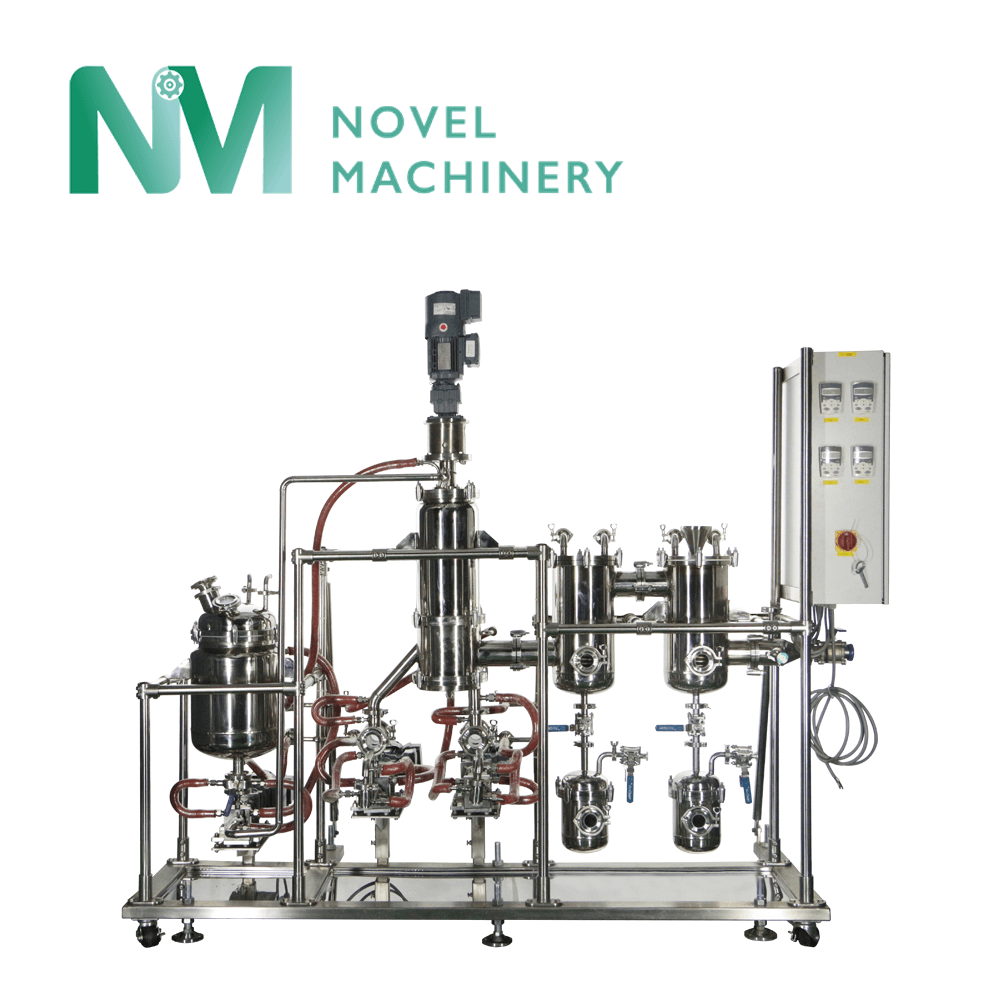
Safety precautions
Danger: Use a power supply that matches the nameplate of the machine, as this will damage the device! Access to equipment must first cut off the power supply, otherwise it will cause electric shock accident!
Danger: The heating circulator must be used to ensure that there is sufficient thermal medium (water or thermal oil) if too low a level will burn the heating pipe and there is a danger of fire! Thermal oil should be used within the specified temperature range!
Danger: Before overhauling electrical equipment or turning on the electrical control box, turn off the total power supply, at the switch need to be left on duty, so as not to cause personnel injury by mishandling!
Warning: Connect the device to the earth, otherwise there will be a risk of electric shock or the risk of static electricity gathering!
Warning: When disassembling the pipes connected between the components of the equipment, the materials in the equipment and lines are first released, so as not to cause material leakage, and to do a good job of protection and collection measures before dissemblying and assembling!
Company Statement
Thank you very much for choosing our company’s single-stage short- range distillation system, from which you will enjoy our quality products and services for you.
Each set of equipment in the factory has been through strict testing and quality inspection, to ensure that every equipment factory is of good quality, please rest assured that the use.
The Company undertakes to provide free repairs within 12 months from the date of shipment, subject to the user’s compliance with the shipping, custody and use rules, in the event of damage due to manufacturing and inability to operate as usual.
We do not undertake to carry out pro bono repairs to products that have been damaged by improper or improper user use and have not been disassembled and disassembled during the warranty cycle without our permission.
Important
Upon receipt of the goods, please check that the equipment is intact, if there is a situation of disability or damage, please inform the delivery person or supplier in order to file a claim.
Please refer to the packing slip to check whether the device and the product you ordered in line with, if not, please contact the supplier in a timely manner.
Prior to installation and start-up, the engineer involved in the installation and maintenance must be familiar with the Operation Service Manual.
It is the user’s responsibility to pay attention to the safety regulations of this manual.
Be aware that common safety regulations include local safety operating procedures.
Installation and maintenance should be strictly in accordance with the existing mechanical, electrical regulations.
Do not disassemble during the warranty period.
Users are responsible for the prescribed operation, regular maintenance, when necessary to replace parts. When there is a clear danger of improper work, it should be stopped in time.
Installation, operation, maintenance, should take into account safety in advance, the use of appropriate tools, protective clothing, goggles and so on.
Failure to comply with these warnings and operating procedures may result in damage and is likely to result in personal injury.
The manufacturer is not responsible for any consequences of violations of the provisions of this Manual.
First, overview
Molecular distillation is a special liquid-liquid separation technique, which is different from traditional distillation based on substance boiling
The spread separation principle is based on the average free range difference of the molecular motion of each substance in the mixture. The principle of the average free range of molecular motion is as shown in the figure on the right In the ideal state, let the liquid mixture flow along the heating plate heating, light, heavy molecules will escape the liquid surface and into the gas phase, because light, heavy molecules of different free range, therefore, the molecules of different substances from the liquid surface after the movement distance is different, if a condensing late can be properly set up, then the light molecules reach the condensing plate is condensed out, and heavy division.The condensate plate cannot be discharged along the mixture. This allows for the purpose of separating the substance. According to this people designed a film-lowering, centrifugal, scraping film and other evaporators, in practice due to each The limitation of seed conditions is difficult to achieve the ideal molecular distillation separation purpose, and all kinds of evaporators have a common characteristic is that the evaporation surface and condensation surface is very short distance, from the evaporation surface overflow molecules to condensation into liquidThe body experiences a short journey, so it is called a short-range distiller.
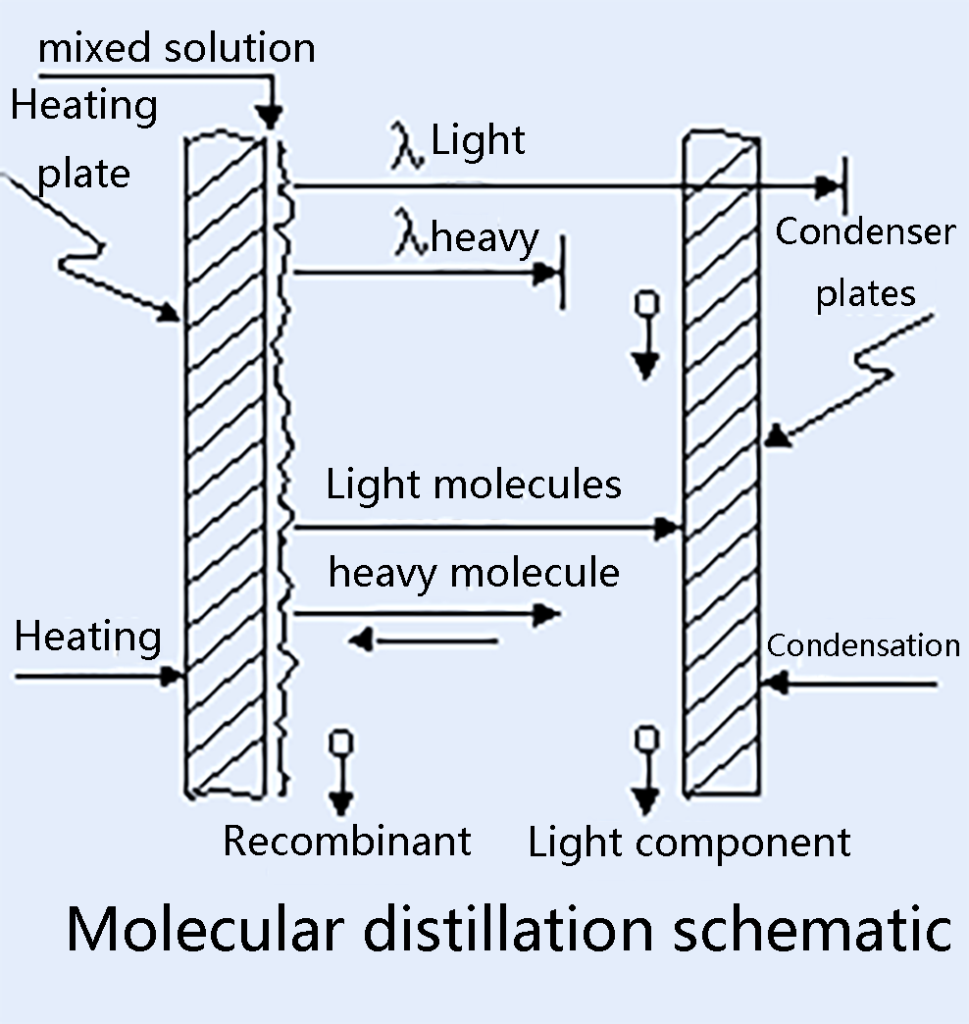
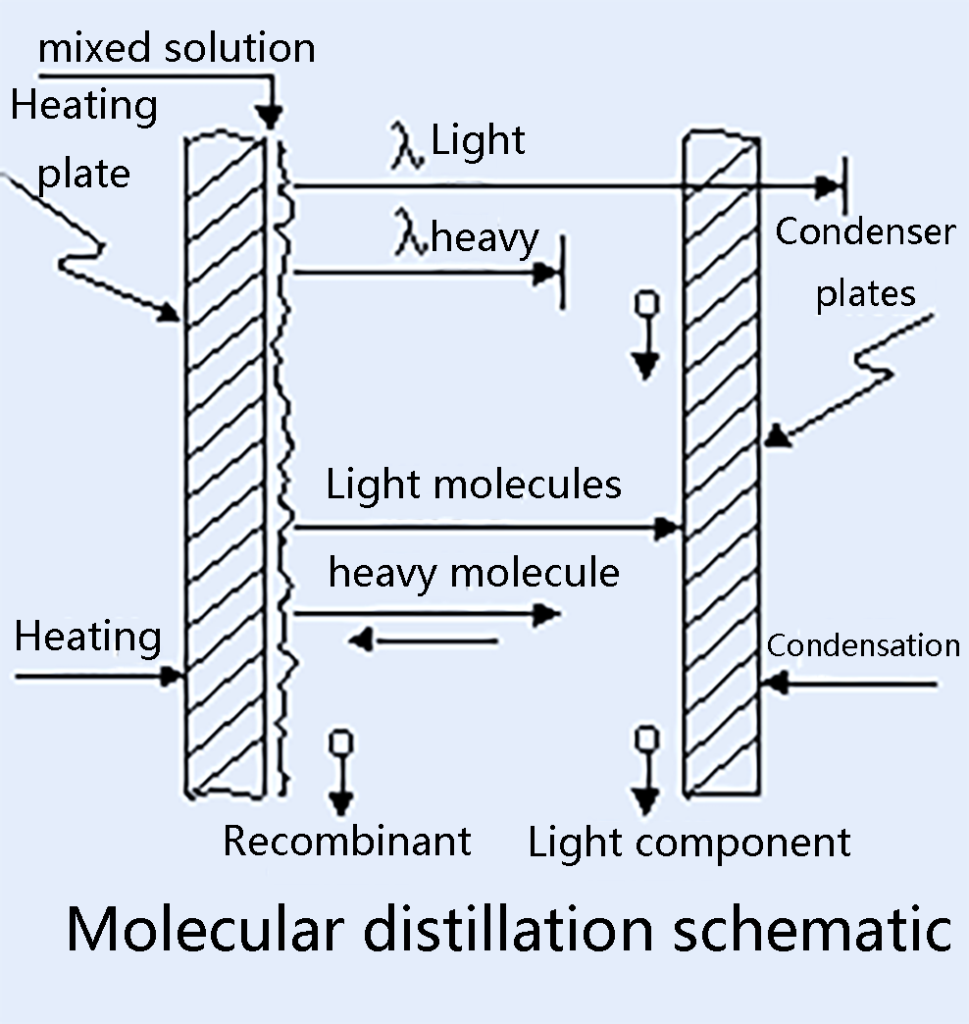
Second,Molecular distillation techniques of special significance
In general, it is very common to use distillation techniques for the separation of liquid substances. Distillation or distillation is a common process, but for many natural products the active substances are easily destroyed during the heating process. In this case, the method generally used is to increase the vacuum level of the system by evacuating it, so that the boiling point of all substances is naturally lowered. This is the way we usually deal with heat-sensitive substances. However, if the active substance is too sensitive to the temperature, then only the extraction method can be used, firstly, the active substance is extracted using the extractant, and then the extractant is separated. But the low boiling point of the extractant is generally toxic, and solvent residue is another problem.
Then there is a short-range distillation technology, here is a brief introduction to the principle. First of all, let’s look at the gas-liquid interface, from a microscopic point of view, our gas-liquid interface is not calm, the molecules in the liquid will briefly leap out of the interface, in these leap out of the interface of a small part of the kinetic energy of the molecules can be diffused into the gas phase, most of the molecules due to the diffusion process and other molecules hitting the loss of energy and then back to the liquid phase. In this way, a diffusion layer is formed near the gas-liquid interface, and the molecular density of this layer is between the gas phase and the liquid phase. The thickness of the diffusion layer is related to the vacuum and temperature. If the vacuum is continuously enlarged, the molecules will be hit less and less frequently, so that the thickness of the diffusion layer will increase, and the proportion of diffusion into the gas phase will be greatly increased. If the liquid phase temperature is high, the molecular energy is large and the thickness of the diffusion layer increases. Finally, in the boiling point state, all the liquid molecules at the gas-liquid interface have the ability to diffuse into the gas phase, at which time it can be assumed that the thickness of the diffusion layer can reach the entire gas phase.


As can be seen from this process above, both reduced-pressure distillation and atmospheric distillation are an equilibrium process, and both have to complete the distillation process at the boiling point corresponding to the pressure. If there is a way to separate the liquid when it reaches below the boiling temperature, then the temperature of the whole separation process can be further reduced, which is the meaning of molecular distillation. The specific way of implementation is divided into come two steps. The first step is still to stretch the vacuum so that the thickness of the diffusion layer will increase. In the second step we put a cooling plate in the diffusion layer very close to the liquid surface. The purpose of this cooling plate is to allow a part of the molecules with higher kinetic energy to enter the diffusion layer, but without the ability to diffuse to the gas phase, to cool down when they hit the plate. This part of the molecules does not have to reach the boiling point to carry out the distillation process.
From a mechanical point of view, the molecular distillation machine now generally uses the scraper type, the specific structure of the following figure, the overall structure is probably two concentric cylinders, the outer cylinder through the heating medium, the inner cylinder through the cooling medium. The fluid flows down from the outer cylinder and is pulled into a liquid film by the scraper. Under the action of vacuum, the liquid in the film makes movement to the gas phase and is cooled down after contacting with the cold inner cylinder to complete the separation process.


The biggest feature of molecular distillation is that the evaporation temperature is lower than that of reduced-pressure distillation, but there are problems, first of all, in terms of mechanism, which is more complicated than conventional distillation, and also difficult to design directly, requiring pre-experiments. Conventional distillation, mainly based on the boiling point and relative volatility of different substances to design, but for molecular distillation, the free range of molecules contribute more to the evaporation process, because the thickness of the diffusion layer of different substances is more influenced by the free range of molecules. Therefore, molecular distillation is a completely different process from conventional distillation. Another thing is that the equipment structure is complex, with rotating machinery and also cooling inner and outer cylinders. In addition the spacing between the inner and outer cylinders is required to be small, while the concentricity of the inner and outer cylinder installation is an issue in large equipment.
Advantages of molecular distillation
Molecular distillation is a non-equilibrium distillation, which is fundamentally different from conventional distillation in terms of its principle. Therefore, it has many advantages that cannot be compared with conventional distillation
(1) low operating temperature:
Conventional distillation relies on the boiling point difference of different substances for separation, while molecular distillation relies on the difference in the average free process of molecular movement of different substances for separation, that is, the latter in the separation process, once the vapor molecules from the liquid phase escape (volatilization can achieve separation, rather than reaching the boiling state. Therefore, molecular distillation is operated far from the boiling point.
(2) Low distillation pressure:
The equation for the mean free range of molecular motion shows that to obtain a large enough mean free range, the distillation pressure must be lowered to obtain it. In addition, due to the unique structure of the molecular distillation unit, the internal pressure drop is extremely small, allowing a high vacuum level to be obtained. Although conventional vacuum distillation can also be used at higher vacuum levels, it is difficult to achieve high vacuum levels due to the internal structure (especially packed towers or plate towers, which have much higher resistance than molecular distillation units). In general, the vacuum level of conventional vacuum distillation is only 5kPa, while the vacuum level of molecular distillation can reach 0.1-100Pa.
As can be seen from the above, molecular distillation is operated under a very high vacuum, and away from the boiling point of the material, so the actual operating temperature of molecular distillation is much lower than conventional vacuum distillation, generally lower than 50-100 ℃.
(3) Short heating time:
Given that molecular distillation is based on the difference in the average free range of motion of molecules of different substances to achieve separation, so the distance between the heating surface and the condensation surface of the device is less than the average free range of motion of light molecules (i.e., the distance is very small, so that the light molecules escaping from the liquid surface almost no collision that reaches the condensation surface, so the heating time is very short. In addition, if the more advanced molecular distiller structure, so that the liquid surface of the mixture to form a thin film, the liquid surface and the heating surface area is almost equal, then the material in the equipment and the residence time is very short. In addition, if the more advanced molecular distiller structure, so that the liquid surface of the mixture to form a thin film, then the liquid surface and the heating surface area is almost equal, then the residence time of the material in the equipment is very short, so the heating time of the remaining material is also very short. Assuming that vacuum distillation needs to be heated for tens of minutes, molecular distillation is heated for only a few seconds or tens of seconds.
(4 degree of separation and high product yield:
Molecular distillation is often used to separate substances that are difficult to separate by conventional distillation, and for substances that can be separated by both methods, molecular distillation has a higher degree of separation. This can be seen from the difference in volatility between the two methods under the same conditions.
(5 In addition, many scholars have studied the factors affecting the heat and mass transfer resistance in the separation process of molecular distillation, and concluded that the separation efficiency is much higher than that of conventional distillation because the liquid film is very thin, and because it operates in a non-equilibrium state, the heat and mass transfer resistance is much smaller than that of conventional distillation.
In view of the above factors, it can be seen that molecular distillation operation temperature is low, the separated substances are less likely to decomposition or polymerization; short heating time, the separated substances can avoid thermal damage; high degree of separation, can improve the separation efficiency. Therefore, in general, the yield of molecular distillation products will be greatly improved compared with traditional distillation.


Full process of short-range molecular distillation
The material obtained after decolorization and concentration is further placed in a short-range molecular distillation apparatus for vacuum distillation. It is known to those skilled in the art that short-range molecular distillation differs from conventional distillation in that it relies on the principle of separation by boiling point difference, and instead relies on the difference in the average free range of molecular motion of the different substances to achieve separation. When the liquid mixture flows along the heating plate and is heated, light and heavy molecules will escape from the liquid surface and enter the gas phase, and because the free range of light and heavy molecules is different, the molecules of different substances will travel different distances after escaping from the liquid surface. In this way, the purpose of material separation is achieved.
The material enters into the short-range molecular distiller for heating under pressure, and a portion of the volatile gas and lighter molecular weight components contained in the material are separated from the remaining heavier molecular weight recombinant fraction products, of which the lighter fraction products contain most of the cannabidiol, which can be further purified by crystallization to obtain cannabidiol products; and the recombinant fraction products contain a small portion of cannabidiol These recombinant fractions were further separated by medium-pressure column chromatography in a simulated moving bed to remove THC, which can be used to obtain the full-spectrum cannabis oil with the appropriate composition according to different needs.


As shown in FIG. 2, in some embodiments, the aforementioned vacuum distillation can also include primary distillation and secondary distillation: the material is heated to 100°C to 130°C for primary distillation, and condensed to 0°C to 60°C to obtain the first light component product and the first heavy component product; where the first light component product includes most of the volatile gases and compounds with molecular weight less than 300, and these light component products are recovered These light component products are recycled. In contrast, the first heavy fraction product contains cannabidiol, as well as other compounds with higher molecular weights.
Then, the first heavy component product will continue to be heated to 100 ℃ ~ 200 ℃ for secondary distillation, condensing to 50 ℃ ~ 70 ℃, to obtain the recombinant fraction product and light component product. The light fraction product contains most of the cannabidiol, which can be further purified by crystallization to obtain cannabidiol products, while the recombinant fraction product contains a small portion of cannabidiol, as well as other cannabinoids, can be further placed in a simulated moving bed for medium pressure column chromatography separation to remove tetrahydrocannabinol (THC), to obtain the full spectrum of cannabis oil.
In some embodiments, the vacuum level of primary distillation is 0 .001 mbar to 1 mbar, preferably 0 .005 mbar, and the scraping speed is 100 rpm to 200 rpm; the vacuum level of secondary distillation is 0 .001 mbar to 1 mbar, preferably 0 .005 mbar, and the scraping speed is 100 rpm to 200 rpm.
According to the present invention, the vacuum distillation is carried out in stages, which can make the separation further complete, so that small molecules and volatile substances are discharged first, further improving the separation and purification of cannabidiol. Compared with traditional separation methods, this method is simpler, more efficient and better purification (content up to 99% or more, recovery up to 75% or more).


Complete sets of devices
A complete set of molecular distillation devices includes:
- Short-range evaporator – Heating system
- Material pre-processing unit – Cooling unit
- Vacuum unit – material collection unit, etc
Performance benefits
- Low evaporation temperature: The liquid distributor and rotating scraper distribute the material evenly on the heating surface in a thin film, reducing the pressure difference generated by the material hydrostatic surface (the vacuum in other evaporation forms only reflects the vacuum degree of the liquid phase body surface in the system),and the vacuum level shown by the system is close to the vacuum degree ofmaterial evaporation The vaporization temperature is greatly reduced due to the increase in vacuum.
- Evaporation strength: the forced action of scraper makes the liquid film in a turbulent state to advance downwards, the self- cleaning effect of scraper inhibits the formation of scale layer on the heating surface, increases the heat transfer coefficient, and improves the evaporation strength.
- Short heating time: The mixture takes only a few seconds to escape from the vaporized condensation or heavy matter added to the lightweight (due to the structure of the evaporator, the amount of feed, the scraping membrane speed, material viscosity, etc.), andis particularly suitable for handling heat-sensitive materials.
- Operation elasticity is large: the unit time into the evaporator material more and less, determines the thickness of the surface of the formation of liquid film, because the scraper
evaporator liquid film is forced to form by scraper, so the feed
volume can be adjusted in a very large range, and then can control the distribution ratio of light, heavy in each component.
Industrial applications
★ thermal separation of thermal compounds
★ purification of organic synthetic substances
★ separation of active ingredients in biological extract
★ recycling of industrial waste
★ the removal of toxic substances from the food industry
★ decolorization of organic compounds, except odor
★ high-precision removal of residual solvents in compounds
Third, the system configuration
Overview of the system
The distillation unit host consists of a feed system, a 0.2m2 short-range evaporator, a two-coil cooling unit, a liquid nitrogen cold trap, and two feeding units; Distilled material is transported to the short-range evaporator by the feed system, the fluid distributor on the rotor is continuously and evenly distributed on the heating surface, and the scraper scrapes the product into a very thin, turbulent liquid film. In this process, the light molecules escaping from the heating surface reach the condenser condense into a liquid, and flow down the condenser tube, through the discharge tube located at the bottom of the evaporator, the active light molecules that are not condensed enter the condenser through the vacuum outlet for secondary condensation;
P@ID flowchart


The list of parts
0.2㎡ Short-range part specification sheet
sequence number | flow chart number | The part name | Size/ Model | Material |
1 | E01 | The main evaporator | 0.2 ㎡ | S31603 |
2 | B01 | Melt tank | 30L | S31603 |
3 | P01 | Feed pump | 4.5CC | Combine materials |
4 | P02 | Feed pump | 4.5CC | Combine materials |
5 | P03 | Feed pump | 4.5CC | Combine materials |
6 | C01 | Process cold trap | S31603 | |
7 | C02 | Double cold trap | S31603 | |
8 | S | The observation mirror | —— | |
9 | Distribution box | The assembly | ||
10 | P | vacuometer | RO-54 | The assembly |
11 | V01 | Insulation ball valve | DN15 | 316L |
12 | V02 | One-way valve | KF25 | 316L |
13 | V03 | One-way valve | KF25 | 316L |
14 | V04 | Vacuum ball valve | KF25 | 316L |
15 | V05 | Vacuum ball valve | KF16 | 316L |
16 | V06 | Vacuum ball valve | KF25 | 316L |
17 | V07 | Vacuum ball valve | KF16 | 316L |
18 | V08 | Vacuum fine- tuning valve | KF10 | 316L |
19 | V09 | Vacuum ball valve | KF40 | 316L |
Device appearance diagram and control key description
- Appearance diagram
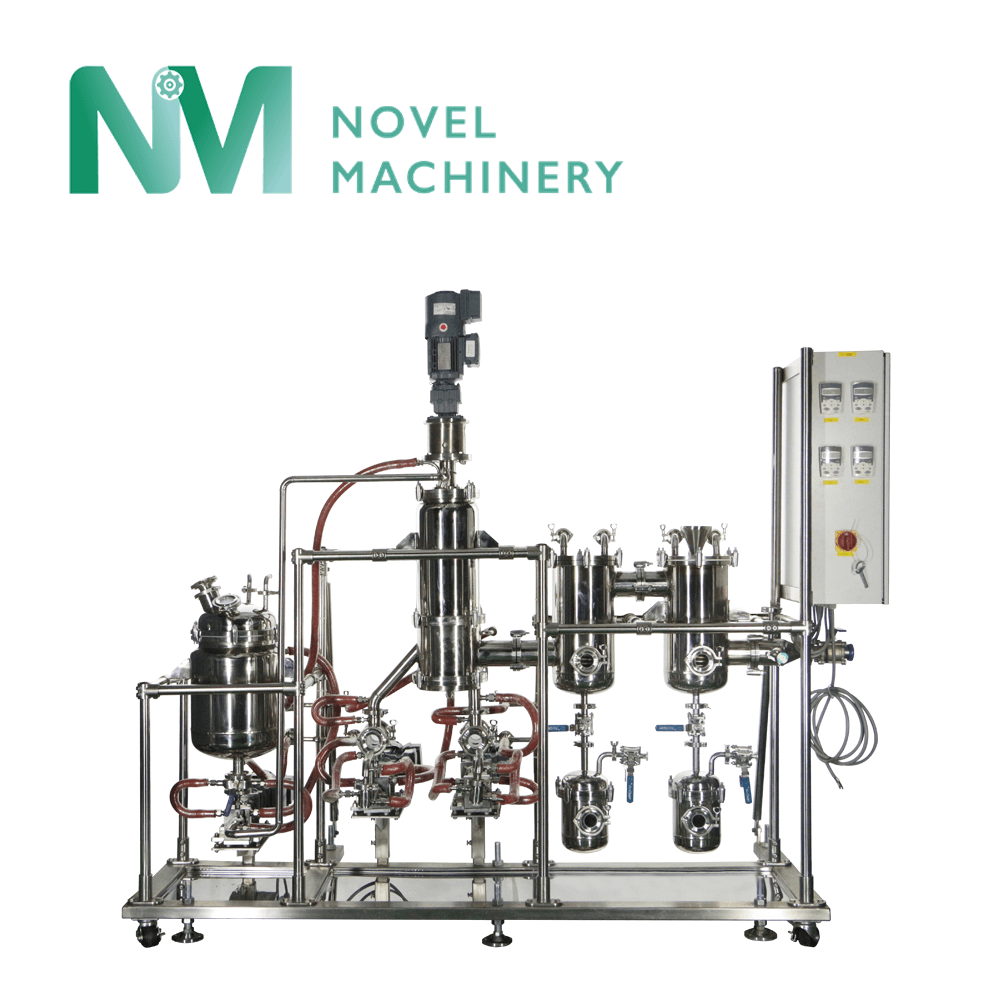
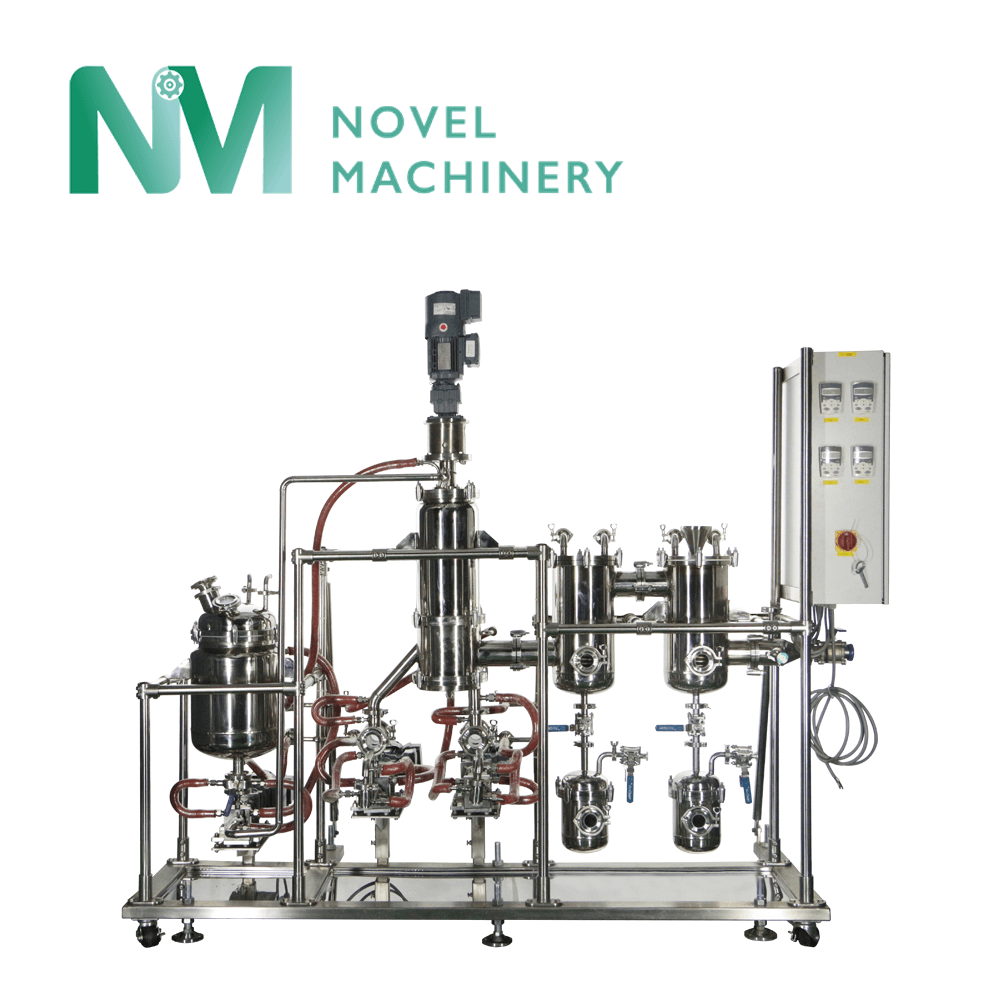
- Control button description


Fourth, daily operation and maintenance
What to know before powering on
- Before use must read and understand the entire set of instructions, the development of power-on status checklist, before power-on to do a status check and confirmation.
- Understand the use of each component method, according to the production process combined with the equipment process to develop operating procedures, the operation personnel for training.
- Equipment operation process needs to be left on duty, in strict accordance with the operating procedures.
- Equipment failure immediately shut down, according to the fault display to judge the fault site and cause, find the relevant professional personnel to correct in a timely manner.
- After the shutdown, water, electricity, etc. facilities need to be turned off and one by one to confirm that each component is in the correct shutdown state.
The process of operation
- Boot
Open the equipment accessory cycle heater and refrigeration unit, etc., according to the product process to set the temperature requirements of each attachment set the relevant equipment operating parameters;
Tip: This process must check whether the components are operating properly and whether the process requirements can be met.
- Fill the item
Add the melted material through the filter to the feeding tank B01. Tip: The filter aperture needs to be less than 200
- The device is running
- Feeding: after the parameters of each component meet the process requirements to start feeding, open valve V01,open P01 adjust the feed speed, open the scraper motor M01,thermal separation process began. Through the mirror S01,S02 observation of light components, recombination distribution, adjust the feed speed and main evaporator temperature so that the distillation ratio to achieve the desired distillation effect.
- Feeding: When the material flows into S01, turn on the discharge pump P03and adjust the discharge speed so that it is equivalent to the speed of light component steaming out. The storage tank B03 material needs to be stopped and emptied before it can be discharged. Tip: In, feed pump is strictly prohibited to idling, scraping film is strictly prohibited for a long time idling, to be distilled material volatile portion should be less than 500ppm.
- stoppage
Follow these steps when a production batch is finished or otherwise down
a Close feed pump P01and close feed valve V01.
b By observing the mirrors S01,S02,turn off the scraper motor M-E01after nolight, heavy and complete outflow.
c Turn off the heating and cooling accessories.
d Emptying the system completely removes material from the equipment.
e Cleaning equipment with a suitable organic solvent during cooling to prevent the high melting point product from solidifying the clogging equipment.
f Turn off the vacuum pump.
g Close all parts.
Special fault
In order to ensure the normal operation of the equipment, the entire internal circulation is in a negative pressure state, when the discharge pump is running normally and can not be materialized, should pay attention to check whether the back pressure valve seal is good at the discharge line, whether there is an internal leakage of the equipment, check the cleaning gas seal pad. (The specific removal method refers to the “Instructions for the use of adjustable spring pressure check valves” below).


Fifth, the gear pump instructions
Company statement
Thank you very much for choosing our company’s gear metering pump, from now on you will enjoy the quality products and services we provide you.
Each gear metering pump in the factory has undergone strict testing and quality inspection, to ensure that every product factory is of good quality, please rest assured that the use.
The Company undertakes to provide free repairs within 12 months from the date of shipment, subject to the user’s compliance with the shipping, custody and use rules, in the event of damage due to manufacturing and inability to operate as usual.
We do not undertake to carry out pro bono repairs to products that have been damaged by improper or improper user use and have not been disassembled and disassembled by us during the warranty cycle.
Important
- Upon receipt of the goods, please check that the equipment is in good condition, in case of disability or damage, please notify the delivery person or supplier in order to file a claim.
- Please refer to the packing slip to check that the device is in compliance with the product you ordered, and if not, please contact the supplier in a timely manner.
- Prior to installation and start-up, the engineer involved in the installation and maintenance must be familiar with the Operation Service Manual.
- It is the user’s responsibility to pay attention to the safety regulations of this manual.
- Be aware that common safety regulations include local safety operating procedures.
- Gear metering pump installation, maintenance should be strictly in accordance with the existing mechanical, electrical regulations.
- Gear metering pumps must only be used under conditions specified at the time of customer ordering, and any changes in operating conditions must be confirmed by the manufacturer.
- The service life of gear metering pumps and related spare parts is limited by wear and corrosion, and faults are affected by the operating environment. Users are responsible for the prescribed operation, regular maintenance, when necessary to replace parts. When the gear metering pump is not working properly or is in obvious danger, it should be stopped in time.
- When installing, operating and maintaining the pump, safety should be taken into account in advance, and appropriate tools, protective clothing, goggles, etc. should be used.
- If the gear metering pump is sold to a third party, the most important thing is to hand this manual over to the new user.
- If you cannot find the information you need in this manual, please contact the supplier.
- Failure to comply with these warnings and operating procedures may result in damage to the gear metering pump and is likely to result in personal injury.
- The manufacturer shall not be liable for any consequences arising from violations of the provisions of this Manual.
Transport and storage
- (1) The gear metering pump must be carefully placed to prevent knocking or damage;
- (2) It is strictly forbidden to place the handle or rope in the position of import and export fittings and couplings during transportation, as shown in Figure 1below(Figure 1 is only a legend, the specific shape is shown in the actual product);
- (3) The storage place must be preservative and kept dry and clean when stored for a long period of time;When not in use for a long time, pump the relevant solvent to flush the pump clean and keep it closed to prevent the conveying material from condensing in the pump.
The installation of the gear metering pump


Figure A diagram of the installation structure of the discharge pump system
- Installation instructions
- The gear metering pump is installed as close as possible to the liquid tank, because the gear metering pump has no self-absorption capacity, the installation should make the gear meter pump import lower than the liquid tank;
- The mounting position of the gear metering pump shall be selected in a bright, dry and clean place for maintenance inspection, and must also be. The space required for removal inspection shall be reserved, and the surface of the installation position shall be clean and flat;
- Gear metering pump design steering is certain, does not allow reversal, so before installation need to understand the import and exit of materials;
- The diameter of the selected connection pipe must not be less than the inner diameter of the fitting, the suction tube should choose a rigid line or skeleton treatment, to prevent a large suction force will suck the import pipe flat;
- The tube must be clean, free of any debris, to prevent foreign material from entering the gear metering pump damaged internal components;
- It is strictly forbidden to have bulging turns or dead corners on the pipeline to prevent gas retention; When installing the import and outlet tubes, we should pay attention to the force of the gear metering pump, otherwise it will affect the use and life of the gear metering pump;
- The pipe connection must be tight to prevent material leakage and gas leakage,so as to ensure the accurate delivery of the gear metering pump;
Special note: Be sure to pay attention to the valve, gear metering pump import and export connection parts of the pipeline sealing, to prevent air from entering the pipeline system, affecting the flow and accuracy of the pump, when the seal is not good the pump will not be normal discharge, and in serious cases will lead to damage to the pump!
- The pump head is fitted with the motor’ connection
If you purchased only the WHT gear metering pump, the structure is shown in the figure:
Follow these steps to install the motor and pump head and take care to check the precautions listed.
- Motor and pump head installation procedures
- The flexible coupling end is loaded into the motor output shaft end and the motor is connected to the base to secure.
- Load the flexible coupling pump joint into the pump input shaft and secure the pump head with the base.
- After installation, the flexible coupling should be able to move smoothly back and forth, such as sliding blocking or stuck indicating that the motor output shaft is different from the pump input shaft, at this time the motor or pump body position to the flexible coupling can move smoothly, in the adjustment should be coiled motor to ensure that the flexible coupling can move smoothly at multiple angles.
- Precautions
- It is best to use flexible couplings to reduce axial thrust and vibration on the pump shaft, thus extending the life of the gear metering pump
The alignment of the pump body and coupling must be accurate.


Flexible coupling diagram
If you purchased our whole pump (pump head, motor, base, coupling and coupling housing are equipped), you do not have to install or adjust the components because we have installed and adjusted them to their optimum condition before shipping The components are recommended that you check the above precautions we have reminded you before starting.
connection
- Wiring must be done by a professionally trained electrician;
- Select the voltage consistent with the motor nameplate;
- The motor overload switch is set at the maximum rated current;
- Connecting control devices;
- Pay attention to good grounding;
- If the motor is a DC motor, do not connect directly to ac electricity.
Initiate
- Check things before starting
- whether the connection of gear metering pump, motor and governor is correct;
- Turn the pump shaft by hand to ensure that it rotates flexibly and without card resistance;
- Make sure that the pump is steered correctly before turning on the motor;
- Make sure that the coupling housing is in place;
- Ensure that the suction tube and the press-out tube are connected correctly and sealed well;
- Start the step
Special Tip: Because the liquid is incompressible, so for the characteristics of different materials, gear metering pump speed should correspond to , so in the first commissioning of the WHT gear metering pump, we must let the gear metering pump start at a lower speed, after the flow is stable, to the desired speed.
Point the motor to see if the gear metering pump is turning correctly and, if not correct, change the way the cable is connected. On the basis of ensuring that the gear metering pump is steered correctly, start at low speed and observe if the pump starts delivering fluid within 15 seconds:
- If you start the delivery, let the gear metering pump turn at low speed until it is turned smoothly and then slowly adjust it to the desired speed, you can start working;
- If the fluid does not start to be delivered within 15 seconds, stop immediately and do not allow the gear metering pump to idling for more than 30 seconds, otherwise it will be possible
Can damage the gear metering pump, recheck the above, if still not, refer to 4.10 Common causes and solutions of failure. If the problem cannot be corrected, contact the pump supplier.
Precautions for use
- Do not operate above design temperature and design pressure without special instructions.
- During use, the liquid surface of the fluid tank should be checked frequently, and the liquid surface should not be too low to cause the pump to dry rotation, pump dry transfer damage shaft seal and other components.
- The transport media viscosity must not exceed the design range of the pump.
- Keep the fluid tank clean so that impurities do not enter the pump and affect the life of the pump.
- If you need to stop for a long time, pump the relevant solvent to flush the pump clean and keep it closed to prevent residual material from condensing in the pump.
- To change the use of the pump and the conveying medium, consult the supplier for technical details.
- If the motor is a DC motor, do not connect it directly to ALTER.
Note: In addition to the above precautions, the following are strictly prohibited behavior, which will lead to gear metering pump acceleration damage!
- The inhale tube is free of fluid when the gear metering pump is started or the valve on the inlet line is not open.
- The valve on the outlet line is closed while the gear metering pump is running, and the pump is depressed.
- The gear metering pump starts at a high speed when pumping liquids with a viscosity greater than 100 cm.
Maintenance and replacement of seals
The seal used in the gear metering pump is the filler seal. If a leak in the sealing area is found during daily use, it should be stopped and checked in a timely manner.
The cause of the leak may be loose filler, please first adjust the cap fixing bolt of the filler seal so that it presses the filler, continue to observe, if the seal leakage, the seal should be.
- Removal of the filler seal
When the filler cap screw is in the end, there is still a leak at the filler, indicating that the filler seal has failed and a new filler needs to be replaced. Follow these steps to remove the invalid filler.
Remove the filler cap;
Remove the filler cavity;
Remove the damaged filler ring in the filler cavity.
The installation of the filler seal
Clean up the filler cap and filler cavity to ensure that the inner wall of the filler cavity is not scratched or damaged;
Install the filler cavity in place and tighten the connection bolts;
Install the filler ring into the filler cavity and the filler ring interface needs to be misaligned.
Fill the filler cap and tighten the cap bolts evenly.
Daily inspection and maintenance
According to the actual situation on the site, arrange a reasonable maintenance table. Here’s what it’s like to check maintenance:
- Listen carefully to whether the gear metering pump and motor have abnormal sound;
- Whether the various connections are loose, leakage;
- Whether there is a significant change in the flow of the gear metering pump.
Instructions for the use of adjustable spring pressure check valves
Adjustable spring pressure check valve is usually installed in the material into the evaporator entrance and outlet position, usually short-range molecular distiller in normal operation of the system inside the negative pressure state, due to the pressure difference inside and outside the system, easy to reflux or reflux phenomenon, which leads to air into the vacuum system internal product pollution, oxidation, the consequences of light will cause serious damage will cause explosions and other production accidents. With the addition of adjustable spring pressure check valves, it is a good way to avoid inversion or reflux.
- How it works
- Through the discharge pump pressurized, when the pressure is greater than the open pressure of the adjustable spring pressure check valve, the valve opens the material outflow, when the discharge pump stops working after the valve automatically resets through the spring pressure, the outlet closes;
- Adjust the opening pressure of the valve by adjusting the spring seat at the bottom;
- The jacket keeps the valve body warm.
- Use and precautions
- Check the valve before installation to see if the hex screws are tightened and if the gasket is broken.
- Rotate the adjustment nut to set the valve opening pressure, pay attention to the setting pressure too much will cause the valve can not open, can not enter and leave the material normally;
- Make sure that the inside of the valve body is clean.
- Common failures and workarounds
- When the discharge pump is working properly but the system is not feeding, check that the valve seal is good;
- When the feed pump is not working but the material enters the equipment or the feed pump is working properly but the feed volume is too large, check that the feed port valve is well sealed.
- Possible causes of common poor sealing
- Broken seals;
- the seal is filled with debris;
- The spring pressure is too small.
Common causes and solutions for failures
fault | possible cause | solution | |
The import and export valve is | Open the import and export valve | ||
not open | |||
Rotate in the opposite direction | Adjust the motor steering to meet the steering | ||
No material | requirements of the pump | ||
is delivered | There is air in the inlet tube | Fill the suction tube with liquid to drain the air | |
Inhalation line damage or gas | Seal the suction line tightly | ||
leakage at the connections | |||
The suction tube or press-out | Clean the suction line and press it out of the line | ||
line is blocked | |||
The material sticks over a large | Reduce the viscosity of the material or the speed of the | ||
amount | pump by heating; | ||
If the viscosity is consistent, contact the supplier if it | |||
is not | |||
Damage to the inside of the gear | Repair or replace the gear pump | ||
pump | |||
The motor speed is too low | Increase the speed of the motor | ||
The valve switch does not open completely | Check the valve, repair or replace it | ||
Inhalation lines damage air | Seal the suction line tightly | ||
Traffic is | leakage at the connections | ||
too small | The suction tube or press-out | Clean the suction line and press it out of the line | |
line is blocked | |||
The suction tube diameter is too | Replace the large diameter of the pipe suction pipe, the | ||
small | diameter of the pipe is slightly larger than the diameter | ||
of the fitting | |||
Inhalation lines have turns or | The suction line should go down smoothly from the liquid | ||
dead corners that leave the gas | bucket to the gear pump | ||
stranded | |||
The press-out tube has a turn or | The press-out tube should go smoothly up from the gear | ||
dead end, leaving the gas | pump to the outlet | ||
stranded | |||
The internal parts of the pump | Repair or replace the gear pump | ||
are heavily worn | |||
The motor is overloaded | The delivery of liquids is highly sticky | Reduce the viscosity of the material or the speed of the pump by heating; If the viscosity is consistent, contact the supplier if it is not | |
The export pressure is too great | Check that the outlet valves are fully open and that the press-out lines are clear; If it is consistent with design pressure, contact the | ||
supplier if it is inconsistent | |||
The inlet foreign material in the pump is stuck | Stop immediately to clean up foreign objects, check for damage to the filter and repair it | ||
The filler pressure is too tight | Adjust the filler press screws | ||
The tooth wheel pump suddenly stops | blackout | Disconnect the motor and wait for an incoming call | |
The motor is under too much load and automatically protects the tripping from power | Find the cause of the overload and follow the plan for the motor overload section | ||
The inlet foreign material in the pump is stuck | Stop immediately to clean up foreign objects, check for damage to the filter and repair it |


For more details, please contact NOVEL machinery!